By Admin
2025-03-27 01:26:07
Customized processing solution for hydrogen energy wire harness
Why choose a professional wire harness factory to customize hydrogen energy wire harnesses?
一、The wiring harness of hydrogen fuel cell vehicles is facing the challenges of "three highs" - high voltage (800V+), high corrosion (hydrogen permeation+acidic environment), and high vibration (fuel cell stack operation impact). Traditional wiring harness factories lack sufficient technical reserves, resulting in:
✅ Cost out of control: The anti-corrosion process does not meet the standard, and the rework rate exceeds 30%;
✅ Delivery delay: Non standard designs rely on manual adjustments, resulting in a 2-3 fold extension of delivery time;
✅ Safety hazard: Poor quality coating causing abnormal resistance, leading to the risk of vehicle recall
二、 Our technological barrier: specializing in customized intelligent manufacturing of hydrogen energy wiring harnesses
1. Material and Process Database
Customer requirements |
industry standard solutions |
our customized solutions |
Resistant to liquid hydrogen corrosion |
Tin plated copper is prone to detachment and has a lifespan of less than 3 years |
Nickel based alloy coating+nano sealing adhesive, with a lifespan of ≥ 8 years |
Lightweight (aluminum wire bundle replacement) |
Aluminum alloy joints are prone to oxidation, with resistance fluctuations of ± 15% |
Laser welding+ceramic coating, resistance stability < ± 3% |
Quick sample delivery |
Mold opening cycle>30 days |
7-day sample production: self owned mold center+3D printing verification |
2. Core Data of Anti corrosion Technology White Paper
- Cost comparison: By adopting our aluminum wire harness solution, the weight of the single bike wire harness system is reduced by 12kg, and the annual production capacity of 100000 units can save material costs of RMB 24 million
- Lifetime verification: Passed 3000 temperature shocks (-40 ℃) ↔ Tested at 120 ℃, the coating showed no cracking (refer to IEC 60068-2-14 standard)
- Customization flexibility: Supports mixed wiring with wire diameters of 0.35mm ²~150mm ², compatible with special terminal standards of BMW, Toyota and other car companies
三、 Customer case: How to achieve a 35% cost reduction for hydrogen heavy-duty truck leaders
Customer pain points:
- The original supplier is unable to meet the pressure resistance requirements of the hydrogen storage tank wiring harness (70MPa dynamic pressure);
- The waterproof rating of the connector is insufficient (only IP65), resulting in a failure rate of over 20% in cold markets.
Our solution:
Structural optimization: Customized corrugated pipe armor layer, with compressive strength increased to 100MPa;
Process upgrade: Adopting dual color injection molding sealing process to achieve IP69 protection level;
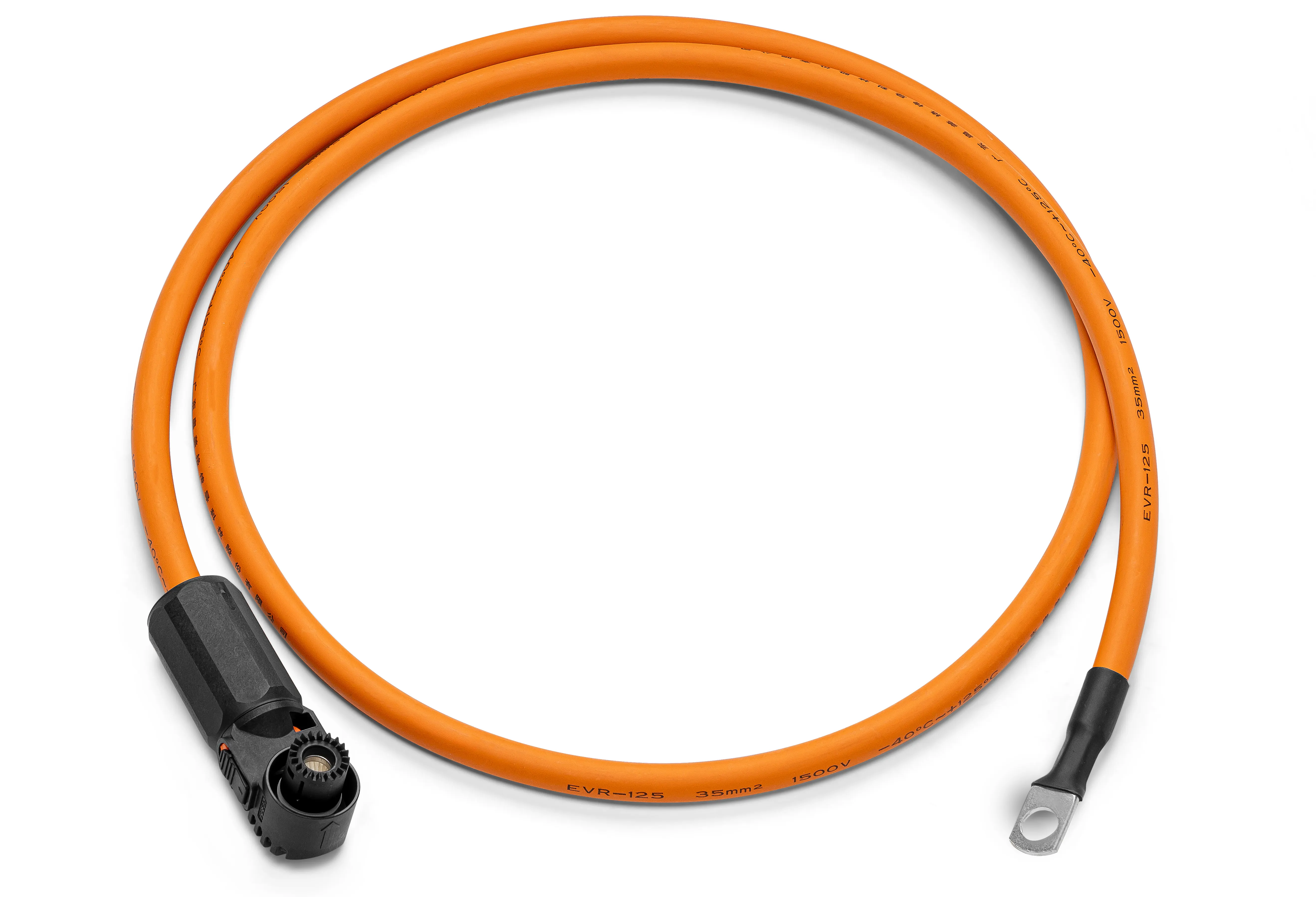
四、 Why can we achieve "high precision+fast delivery"?
Production process |
industry average |
Our customized production line capability |
Cutting accuracy |
±0.5mm
|
± 0.1mm (laser measurement calibration) |
Terminal crimping |
Yield rate of 92% |
99.3% yield rate (AI visual real-time monitoring) |
Quality inspection efficiency |
3 people/hour (manual sampling) |
2000 points/second (automated electrical performance testing bench) |
Flexible delivery system
- Small batch orders: minimum order of 3 items, supporting customer logo marking and independent packaging;
- Intelligent production line: We are equipped with advanced automation machines and digital management systems to ensure a cutting accuracy of ± 0.1mm, a terminal crimping yield rate of 99.3%, and a quality inspection efficiency of up to 2000 points per second.
- Transparent traceability: Each wire harness has an independent QR code, which can be used to check the raw material batch/processing personnel/test data.
五、 Core technological advantages: customized intelligent manufacturing and material innovation
1. Advanced materials and processes
We provide high-performance cable materials including UL1007, UL1015, and apply advanced processes such as nano ceramic coatings and high-strength aluminum alloys to ensure the long-term stable operation of wire harnesses in hydrogen environments. Support customization of various functional wiring harnesses including waterproofing, I/O data transmission, high and low voltage conversion, etc., widely applicable to industrial equipment, automobiles, robots, medical equipment and other fields.
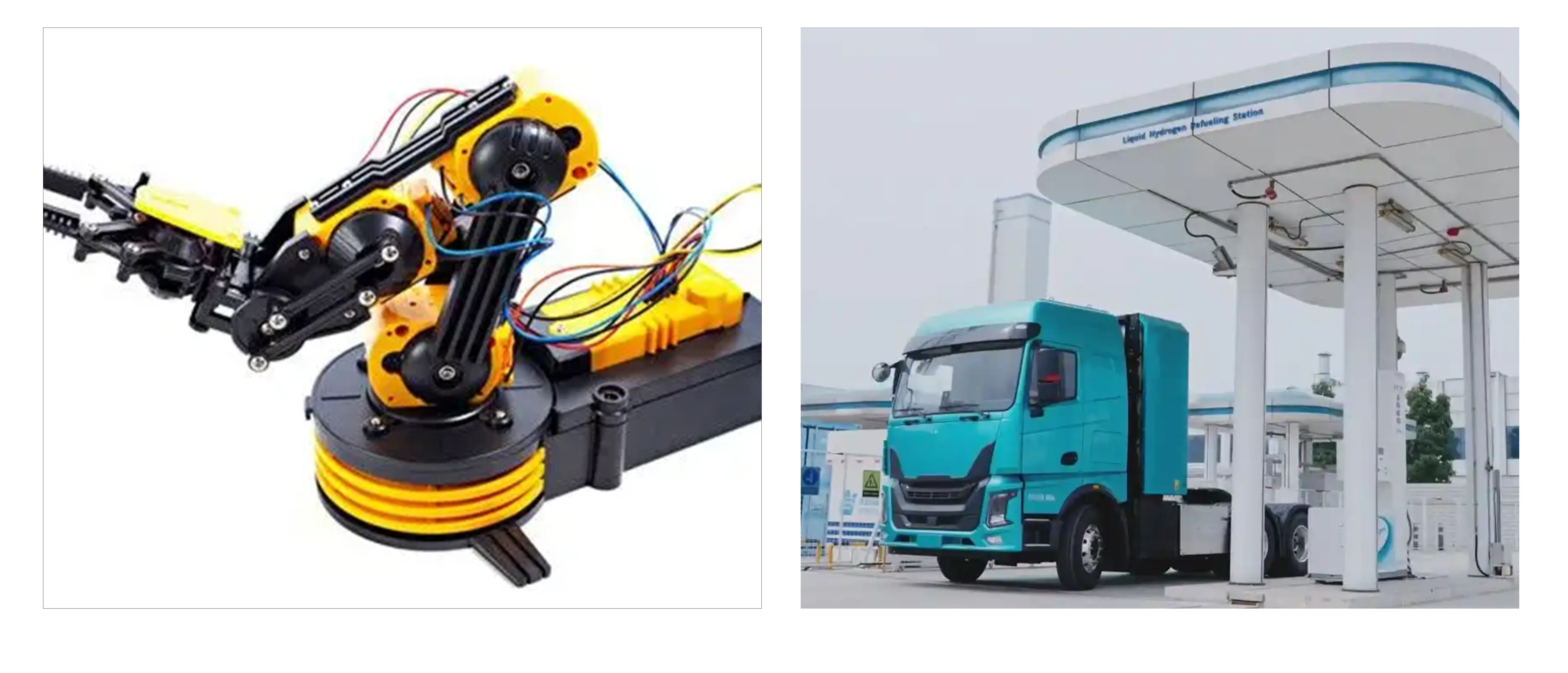
2. Overview of anti-corrosion technology
- Material selection: Cable materials specifically designed for hydrogen environments, such as copper aluminum composite materials with special coatings, are used to enhance corrosion resistance.
- Process optimization: Ensure that every step of the manufacturing process meets the highest standards through PFMEA (Process Failure Mode and Effects Analysis) and QCP (Quality Control Plan).
- Performance testing: Strict MPI (Manufacturing Process Inspection) and SIP (Standard Inspection Procedure) ensure that the product meets or exceeds international standards such as ISO9001 and IATF16949.
六、 Choose our 3 main reasons
- Technological Leadership: Certified according to international standards such as ISO9001 and IATF16949 to ensure product quality.
- Cost effectiveness: Collaborate with top global material suppliers to optimize procurement costs.
- Service guarantee: 24/7 response mechanism, on-site handling of quality issues within 48 hours.
Contact Us
📞 Customized hotline: 86076983991366
🌐 Official website direct access: [www.kaweei.com]
📧 Engineer support: [email protected]