By Admin
2025-02-13 05:41:52
Comprehensive Guide to Custom 4Pin Housing with Terminal Cable Assembly: Materials, Manufacturing, and Applications
1. Material Selection for 4Pin Cable Assembly
- The performance of a wire harness hinges on its material quality. Below are the key components:
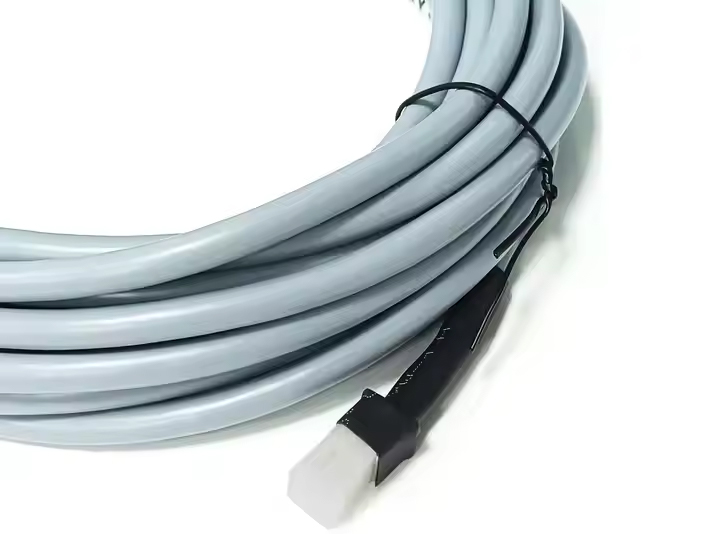
1.1 Conductor Materials
- Copper: The primary choice for conductors due to its high conductivity, solderability, and corrosion resistance. Copper wires ensure minimal energy loss and stable signal transmission, making them ideal for automotive and industrial applications.
- Aluminum: A lightweight alternative for weight-sensitive applications, though less durable than copper.
- Silver-Plated Wires: Used in high-end assemblies for superior conductivity and oxidation resistance.
1.2 Insulation Materials
- PVC (Polyvinyl Chloride): Cost-effective with excellent electrical insulation, oil resistance, and abrasion tolerance. Widely used in standard wire harnesses.
- PE (Polyethylene): Offers better temperature resistance (-60°C to 80°C) and environmental stability, suitable for harsh conditions.
- PTFE (Polytetrafluoroethylene): Ideal for extreme temperatures and chemical exposure, though higher in cost.
1.3 Housing and Terminal Materials
- Nylon/PBT Housing: Provides mechanical strength, heat resistance, and waterproofing for automotive and outdoor applications.
- Brass/Tin-Plated Terminals: Ensures secure connections and corrosion resistance. Terminals are precision-engineered to match Molex or JST standards for compatibility.
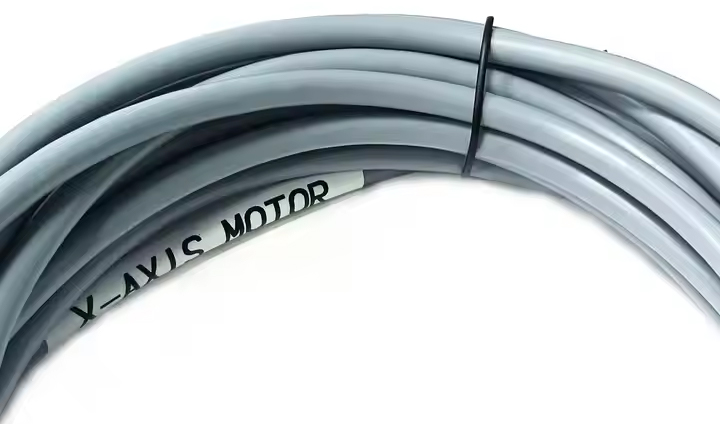
2. Manufacturing Process of 4Pin Cable Assemblies
- The production involves stringent processes to ensure reliability and compliance with industry standards.
2.1 Cutting and Stripping
- Wires are cut to specified lengths using automated machines.
- Precision stripping removes insulation without damaging conductors. Critical parameters include strip length tolerances (e.g., ±0.2mm) and smooth cut edges.
2.2 Terminal Crimping
- Terminals are crimped onto stripped wires using hydraulic or pneumatic presses. Proper crimp height and pressure are monitored to avoid under/over-crimping, which could lead to connection failures.
- Quality checks include pull-force testing (e.g., 15N minimum for automotive connectors) and visual inspection for crimp integrity.
2.3 Housing Assembly
- Terminals are inserted into 4Pin housings, ensuring correct orientation and audible "click" confirmation. Automated insertion machines enhance consistency.
- Waterproof variants include over-molded seals or silicone gaskets to prevent moisture ingress.
2.4 Testing and Validation
- Electrical Testing: Continuity, insulation resistance (≥100MΩ), and dielectric strength (e.g., 500V AC for 60 seconds).
- Environmental Testing: Exposure to temperature cycles (-40°C to 125°C), vibration, and salt spray to simulate real-world conditions.
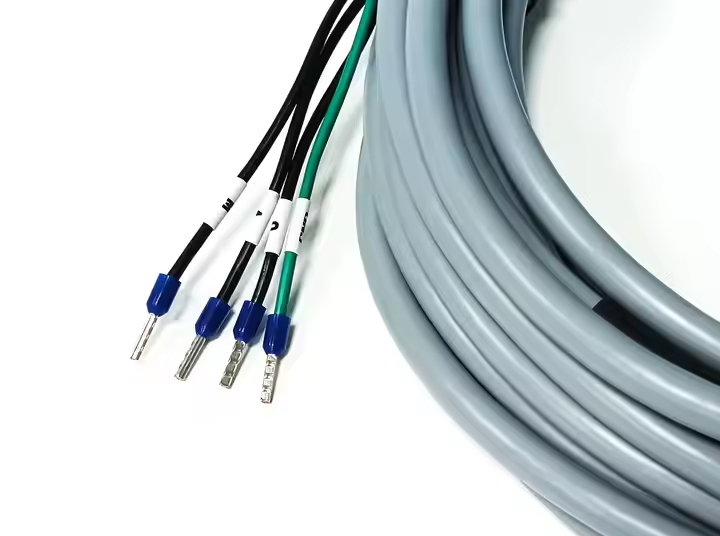
3. Applications Across Industries
3.1 Automotive Systems
Used in rear-view cameras, ECU connections, and infotainment systems. Automotive-grade assemblies meet ISO 16750 and SAE J1128 standards.
Example: STONKAM’s 4Pin extension cables for vehicle cameras ensure stable video transmission in harsh environments.
3.2 Industrial Automation
Connects sensors, PLCs, and robotic arms. Overmolded designs withstand dust, vibration, and EMI interference.
3.3 Consumer Electronics
Powers drones, gaming consoles, and smart home devices. Compact 4Pin connectors enable space-saving designs.
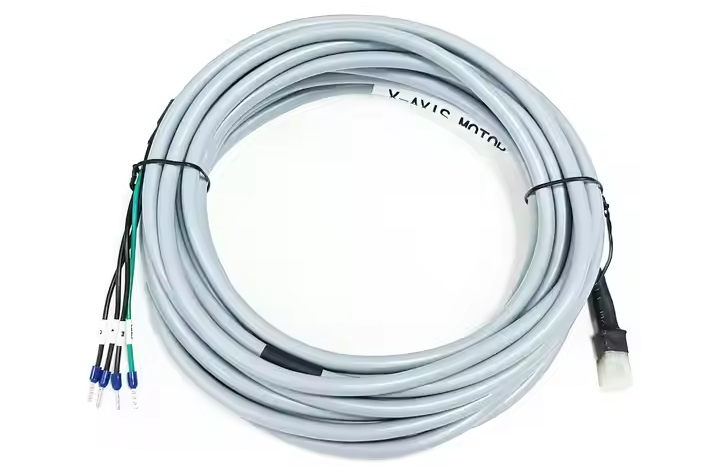
4. Advantages of Custom 4Pin Assemblies
- Customization: Tailored wire lengths, colors, and shielding (e.g., braided or foil) for specific applications.
- Durability: IP67-rated waterproofing and UV-resistant materials for outdoor use.