By Admin
2025-03-15 08:48:24
Customized High-Voltage Harness Solutions
High voltage wiring harness is an integrated solution designed specifically for high-voltage electrical systems, mainly used in fields such as new energy vehicles and industrial equipment to meet the needs of high-voltage power transmission, equipment connection, and safety protection.
1、 Definition and Function
- Basic concept: High voltage harness refers to a wire harness and related components used for transmitting high voltage (usually above 62V DC), consisting of wires, connectors, insulation layers, shielding layers, etc.
- Core function: To achieve efficient transmission of electrical energy in high-voltage systems, while ensuring electrical safety through insulation, shielding, and other technologies
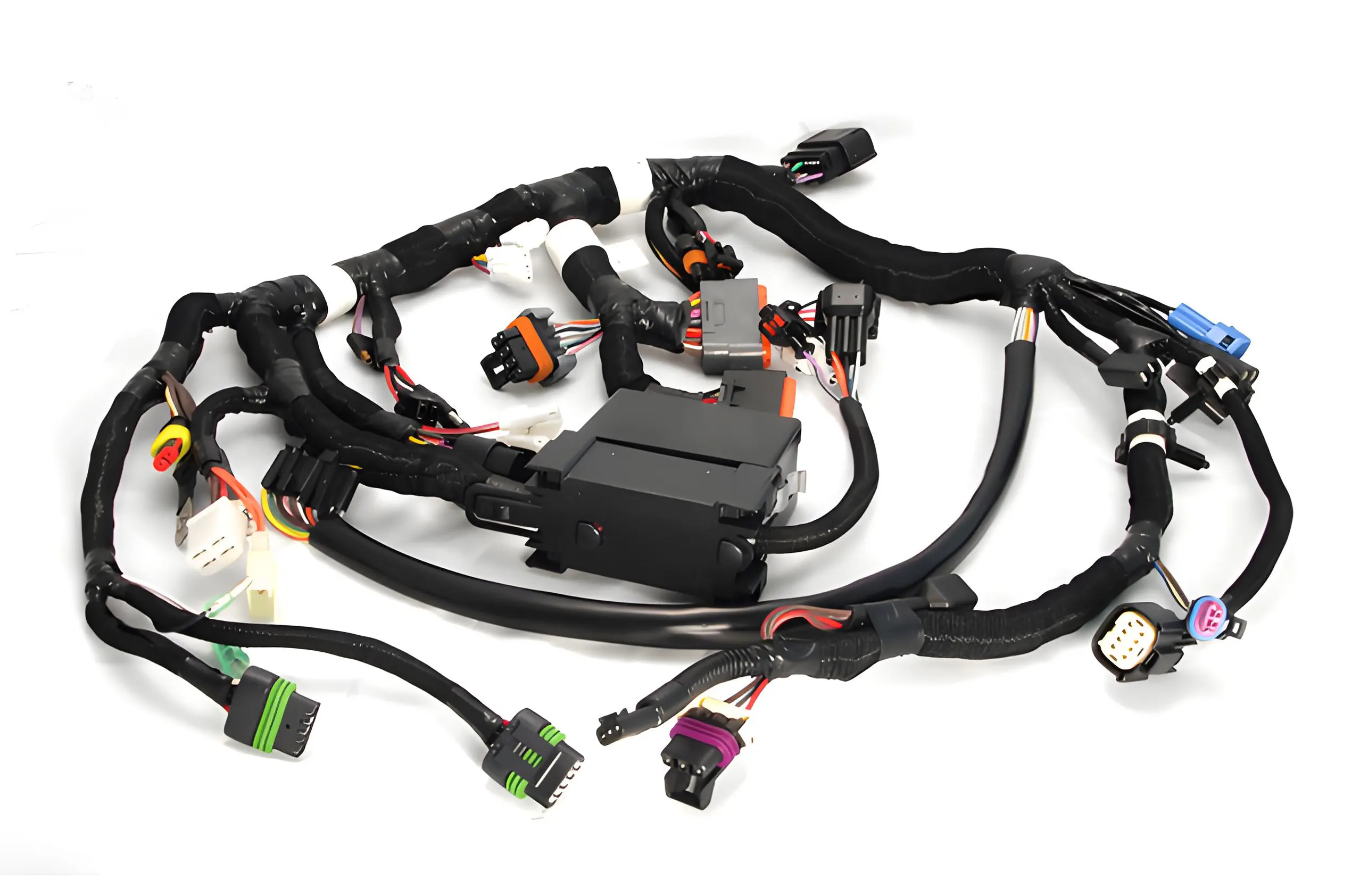
2、 Core Composition and Technology
Materials and Structure
- High temperature resistant material: Made of silicone rubber and other organic silicon materials, it has high temperature resistance (-73 ℃ to 180 ℃), corrosion resistance, and is suitable for high temperature environments such as engine compartments.
- Shielding design: Reduce electromagnetic interference and ensure signal transmission stability through multi-layer insulation and metal shielding layers.
- Flexible wiring: The wiring harness needs to have high flexibility to adapt to the narrow space and complex wiring requirements of vehicles.
Safety standards
- Voltage withstand test: The insulation performance needs to be verified through high-voltage insulation tests (such as electrical strength tests, breakdown flicker tests).
- Current/voltage mode control: Combining voltage source and current source regulation mechanisms to prevent overload or short circuit risks.
Fast charging support
- Support 800V high-voltage fast charging architecture, reduce resistance and improve charging efficiency through highly conductive materials and optimized wiring.
3、 Main application areas
New energy vehicles
- Connect core components such as power batteries, drive motors, and high-voltage distribution boxes to undertake the task of distributing high-voltage electrical energy.
Industrial equipment
- Used for internal connections of high-voltage power sources (such as 50V-600kV) and power transmission equipment.
Charging infrastructure
- Provide high reliability wiring harness for fast charging piles to meet the transmission needs of high current and high voltage.
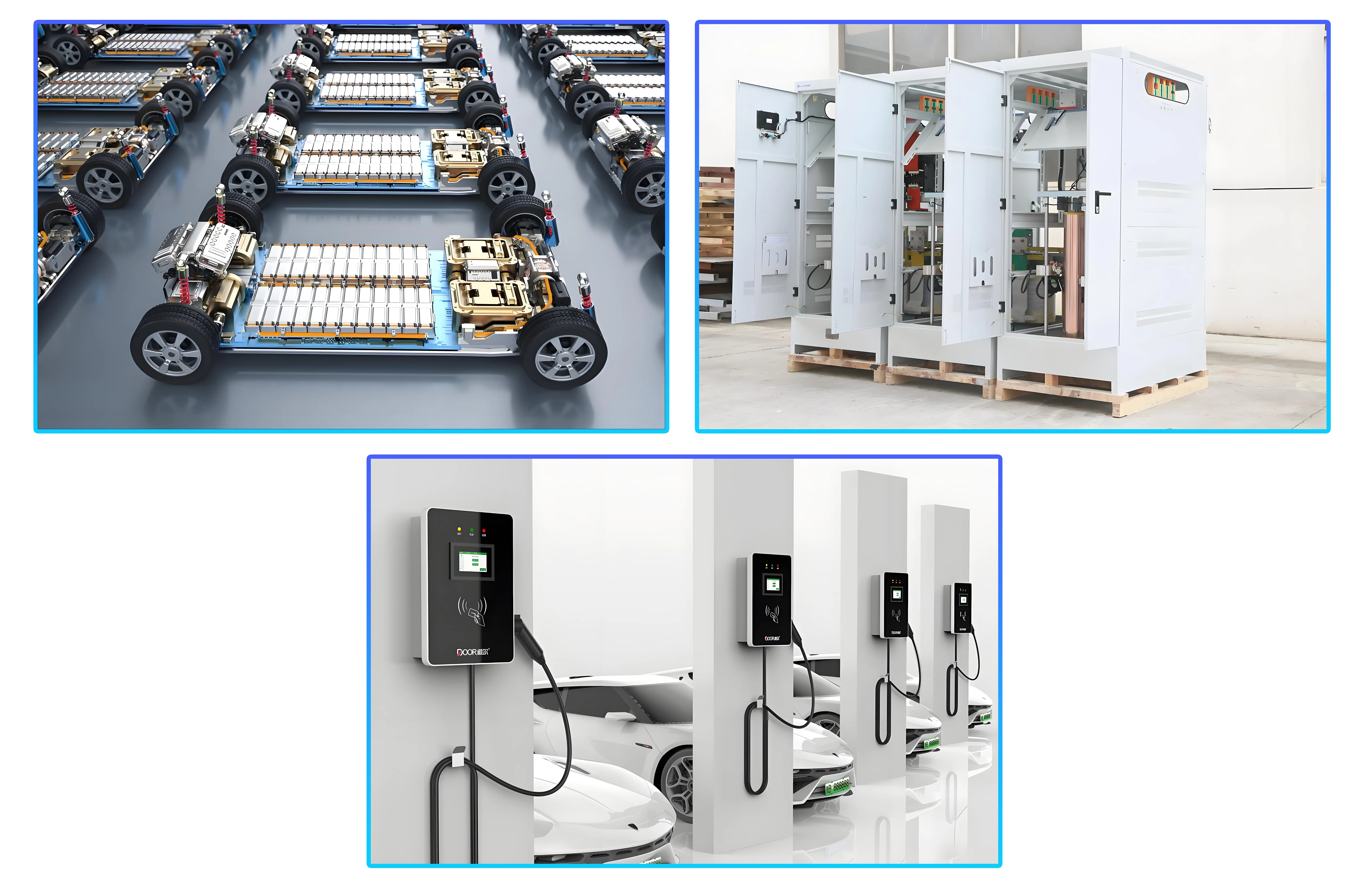
Core Features: Built for Reliability
To meet the rigorous demands of new energy vehicles, these harness assemblies prioritize:
- High-Temperature Resistance: Silicone-insulated cables withstand 150°C+ environments near powertrains and battery packs.
- Vibration Resilience: Reinforced connectors (e.g., AMPSEAL or Deutsch HD series) prevent loosening in rough terrain.
- EMI Shielding: Triple-layer braided shielding protects low-voltage control signals from high-current interference.
- Modular Design: Plug-and-play architecture simplifies maintenance for fleet operators.
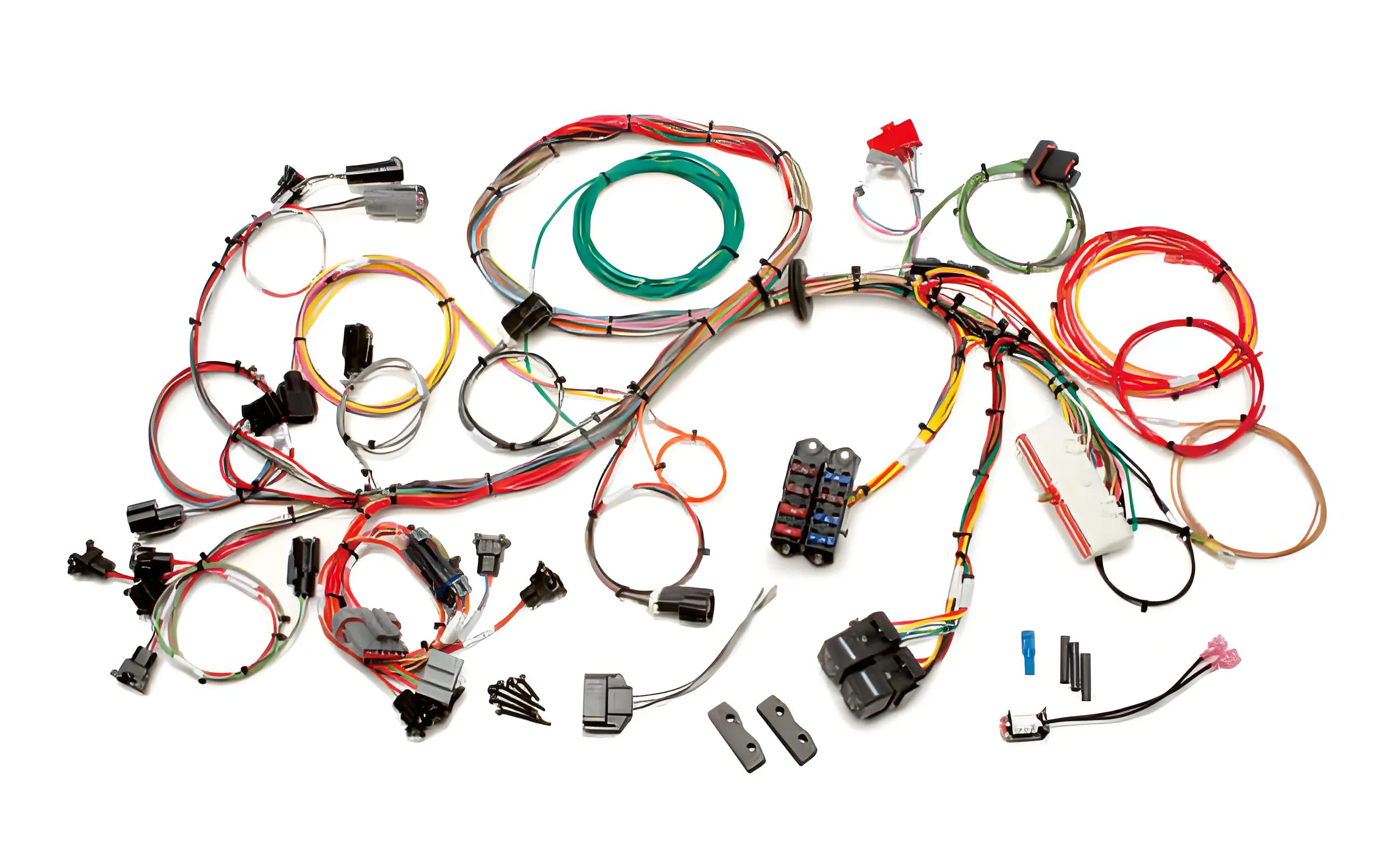
Kaweei’s Tailored Expertise
As a leader in new energy vehicle harness manufacturing, Kaweei bridges innovation with industrial pragmatism:
1. Scenario-Driven Customization:
- Design harnesses for specific accessory layouts (e.g., rooftop AC units in electric buses).
- Optimize wire gauges (16–50 mm²) to balance current capacity and weight savings.
2. Certified Scalability:
- Pre-validated harness kits with ISO 19642 and RoHS documentation accelerate OEM integration.
- Batch production with ±2% tolerance control reduces per-unit costs for large fleets.
3. Rapid Prototyping:
- 3D harness modeling elivery streamline R&D cycles.
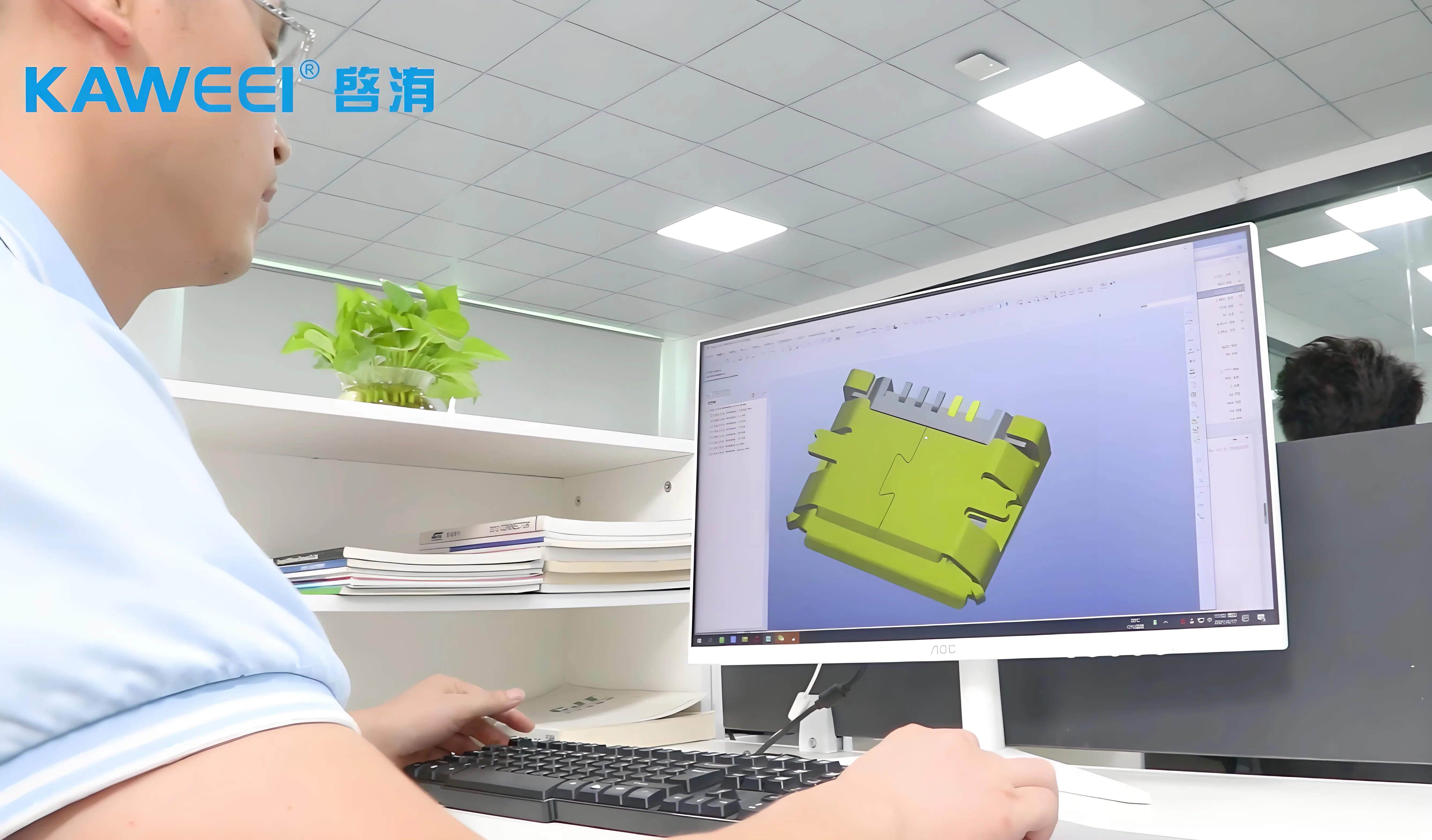
For over a decade, Kaweei has been dedicated to customizing wire harness and cable components, providing professional connection solutions for industrial equipment, telecommunications, healthcare, vehicles, and other fields. Kaweei has obtained ISO quality certification, efficient production efficiency, and specialized customized services, ensuring that every electric truck or bus can provide unparalleled comfort, safety, and operational efficiency.