By Admin
2025-02-12 01:08:35
Motor Vehicle Wiring Harness: Materials, Manufacturing, and Industrial Applications
1. Product Overview: Motor Vehicle Wiring Harness
A motor vehicle wiring harness is a structured assembly of wires, connectors, and terminals designed to transmit power and signals within automobiles. Key features include:
- Durability: Resists vibrations, temperature fluctuations (-40°C to +125°C), and chemical exposure.
- Customization: Tailored for specific vehicle models, from compact cars to heavy-duty trucks.
- Safety Compliance: Meets ISO, UL, and RoHS standards for flame resistance and environmental safety.
Applications span engine management systems, infotainment, lighting, and advanced driver-assistance systems (ADAS).
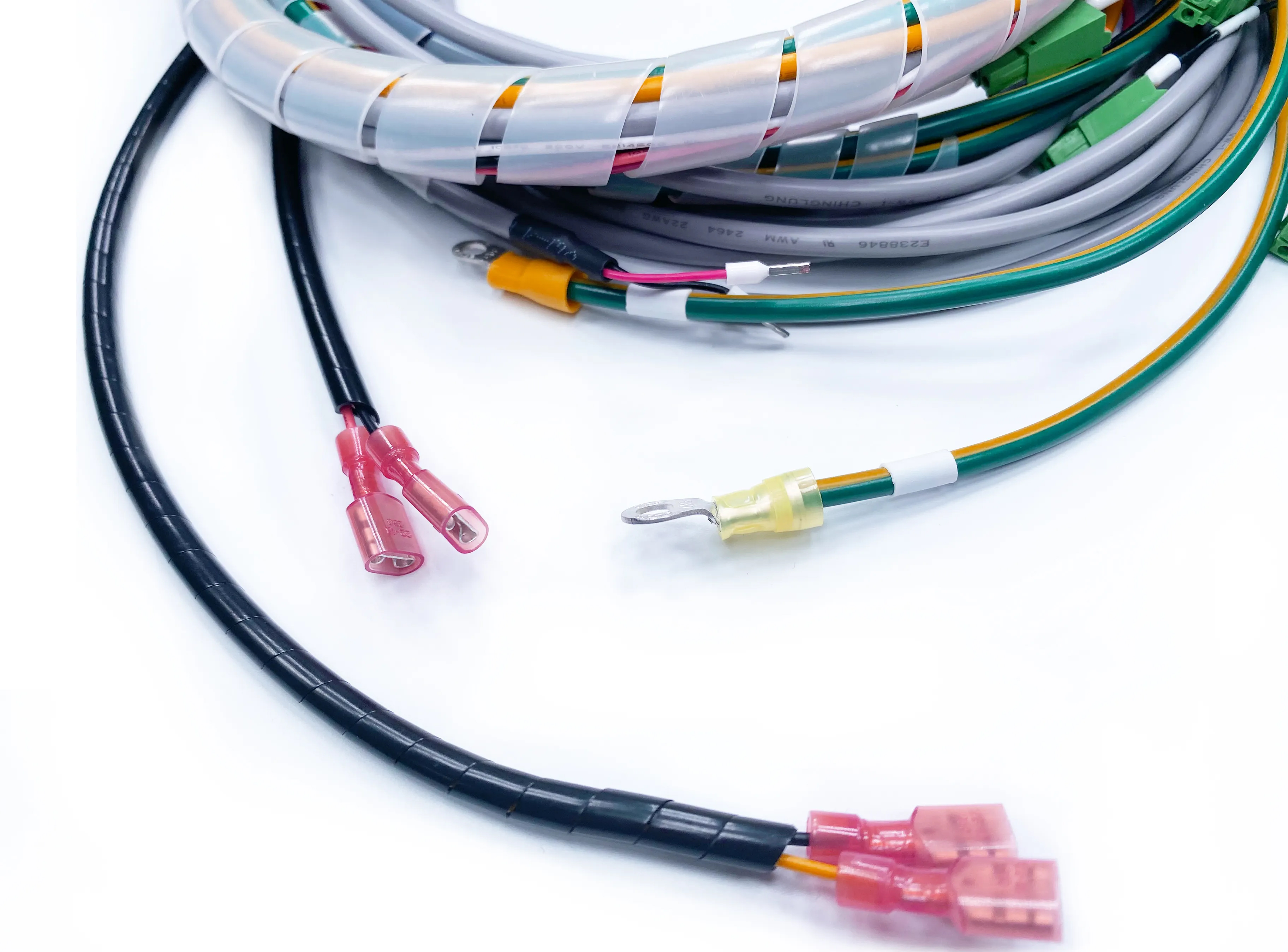
2. Materials and Construction
A. Conductors
- Copper Alloys: High conductivity (≥98% IACS) and flexibility, ideal for signal transmission.
- Tinned Copper: Enhances corrosion resistance in humid or saline environments.
B. Insulation and Sheathing
- PVC (Polyvinyl Chloride): Cost-effective and flame-retardant, suitable for low-voltage applications.
- Cross-Linked Polyethylene (XLPE): Withstands high temperatures (up to 150°C) in engine compartments.
- PTFE (Teflon): Used in high-frequency applications (e.g., radar sensors) due to low dielectric loss.
C. Connectors and Terminals
- Zinc Alloy Housings: Provide EMI shielding and IP67 waterproofing for under-the-hood use.
- Gold-Plated Contacts: Ensure reliable signal integrity in ADAS and infotainment systems.
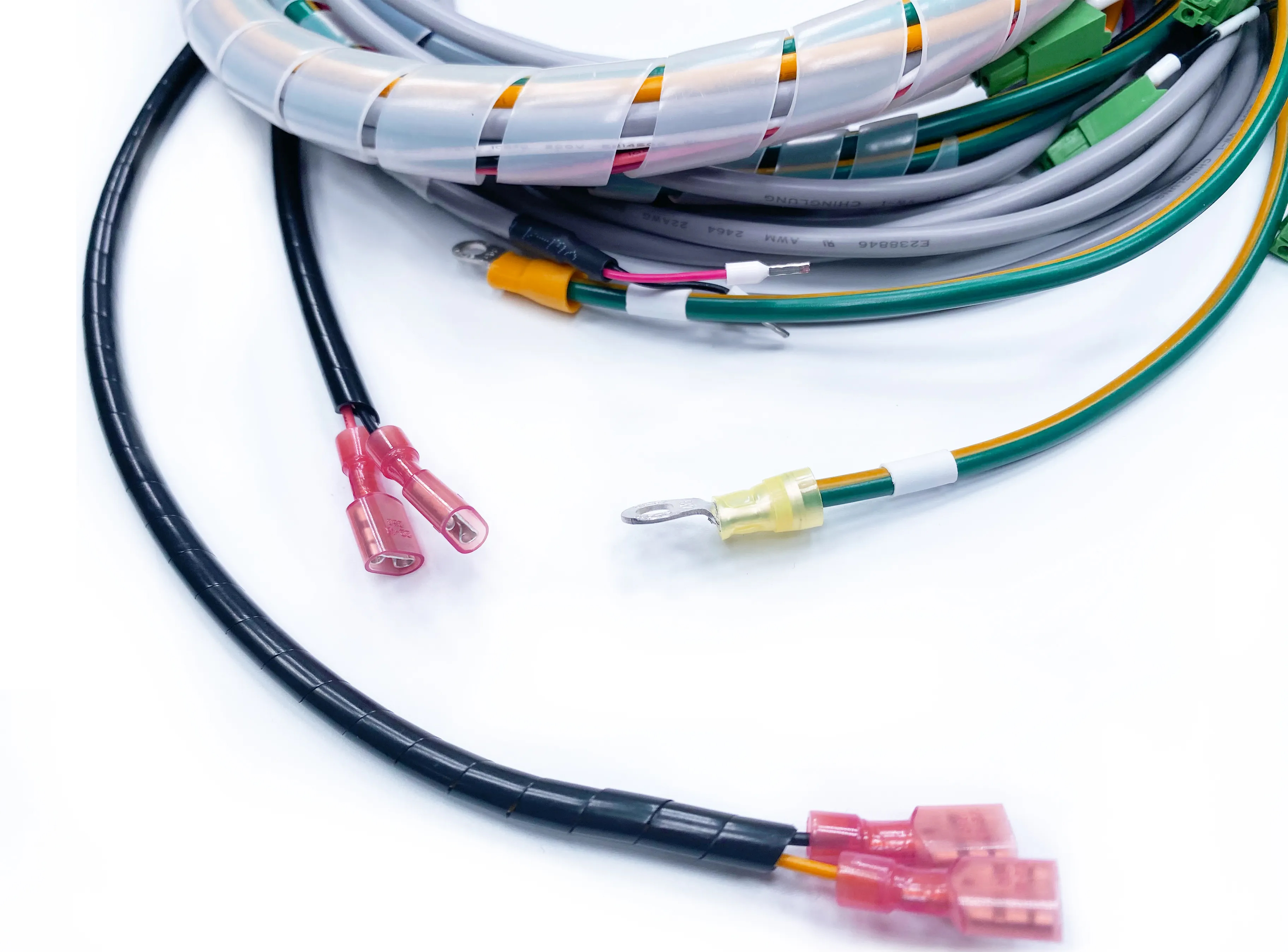
3. Manufacturing Process
A. Wire Cutting and Stripping
Precision laser cutting ensures uniform wire lengths, while automated stripping machines remove insulation without damaging conductors.
B. Crimping and Soldering
- Ultrasonic Welding: Creates gas-tight connections for high-current applications (e.g., EV battery harnesses).
- Automated Crimping: Robots apply consistent pressure to terminals, reducing human error.
C. Harness Assembly
- Modular Design: Sub-harnesses (e.g., engine, door panels) are pre-assembled for efficient installation.
- Overmolding: Thermoplastic elastomers (TPE) encapsulate connectors for vibration resistance.
D. Quality Testing
- Hi-Pot Testing: Verifies insulation integrity at 1.5–3kV.
- Continuity Checks: Ensures zero open circuits or short circuits.
Leading manufacturers like Amphenol DC Electronics employ lean manufacturing and IPC-620 Class III standards for aerospace-grade reliability.
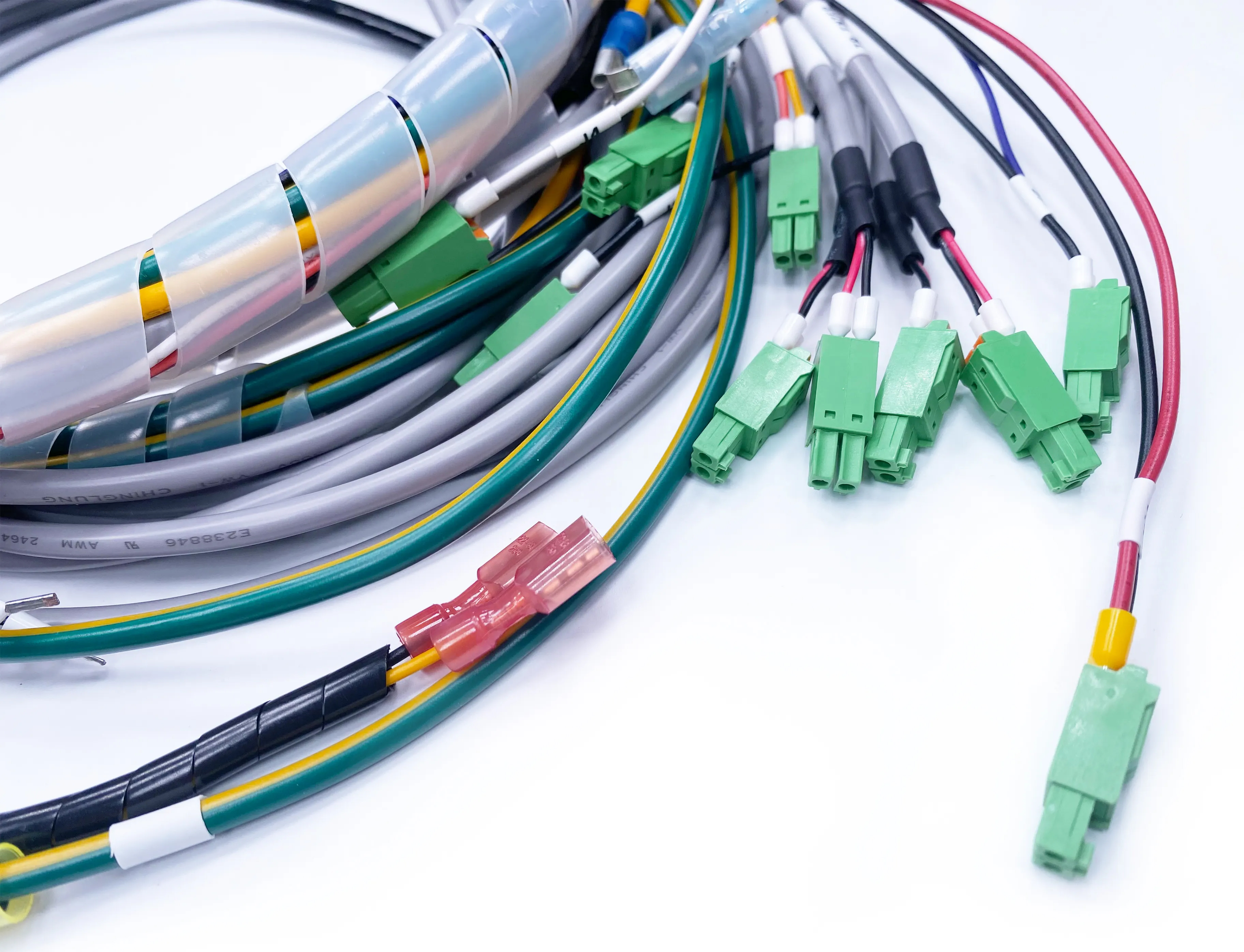
4. Applications in Automotive Systems
A. Engine and Transmission
- Fuel Injector Harnesses: Customized for high-pressure environments with PTFE insulation.
- Sensors and Actuators: Shielded cables prevent EMI interference in turbocharger controls.
B. Electric Vehicles (EVs)
- Battery Management Systems (BMS): High-voltage harnesses (up to 800V) use XLPE insulation for thermal stability.
- Charging Ports: IP67-rated connectors ensure waterproof performance.
C. ADAS and Autonomous Driving
- Radar and LiDAR: Low-noise cables with gold-plated contacts maintain signal accuracy.
- Camera Modules: Miniaturized connectors (e.g., JST ZH series) save space in compact designs.
5. Industry Trends and Innovations
- Lightweight Materials: Aluminum-coated wires reduce harness weight by 30%, improving EV range.
- Smart Harnesses: Integrated sensors monitor wire health, predicting failures via IoT connectivity.