By Admin
2025-04-07 01:58:41
What is a marine wiring harness
Marine wiring harness is a systematic component used on ships to integrate, connect, and fix cables, pipelines, and electrical equipment. It consists of multiple cables, connectors, protective layers, etc. and serves power transmission, signal control, communication, and safety systems. It needs to meet special environmental requirements such as waterproofing, anti-corrosion, and pressure resistance.
Core Structure and Composition
Types of cables and pipelines |
Cable material |
protection structure |
Protection level |
Power Cable |
Shielded coaxial line (RG series) |
Waterproof rubber/silicone |
IP67 and above |
Signal cable (communication system) |
optical fiber |
Sealing shaft/sleeve assembly |
Salt spray resistant environment |
Hydraulic pipeline |
Flame retardant material |
Mechanical card slot/limit hole design |
Adapt to high humidity conditions in the cabin |
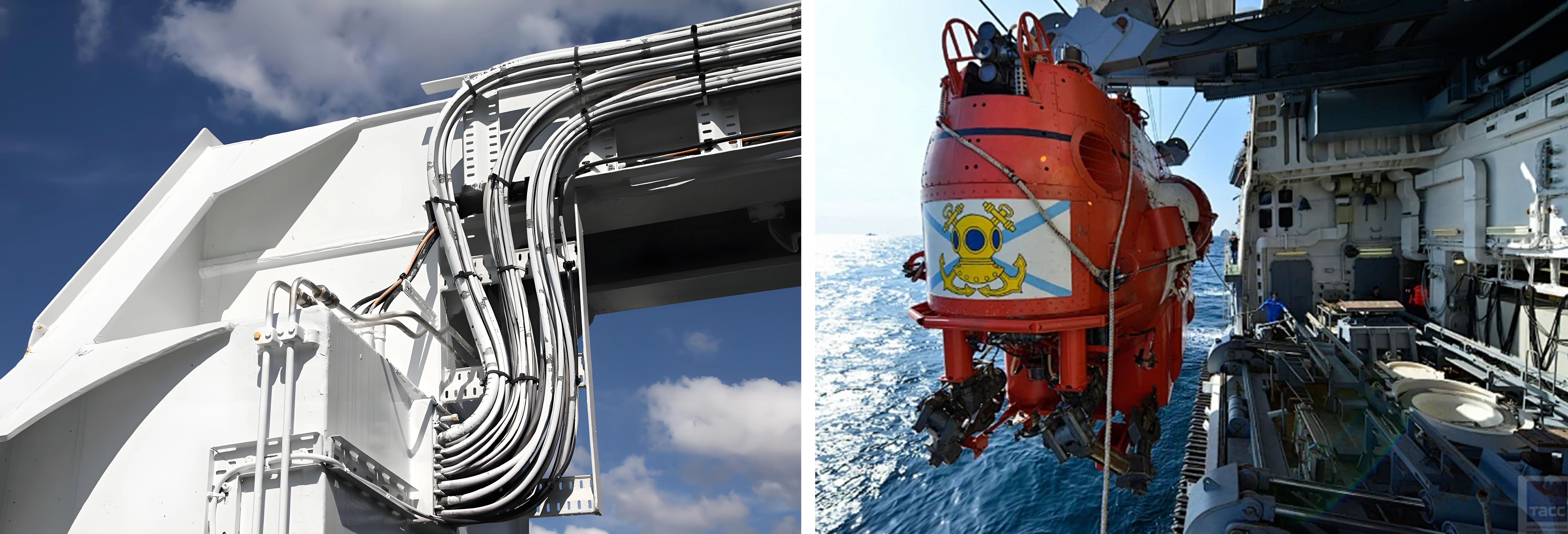
Technical points
- Environmental adaptability: It is necessary to pass anti salt spray and anti oil pollution tests to avoid corrosion in marine environments.
- Space optimization: When designing, it is necessary to consider the limitations of ship space and use lightweight materials and compact layouts.
- Maintenance convenience: Adopting modular design (such as split sleeve and limit hole structure), it is easy to inspect and replace.
Special requirements to be considered in the design of marine wiring harnesses
1、 Environmental adaptability requirements
Waterproof and anti-corrosion
- Waterproof rubber, silicone or flame-retardant materials should be used to wrap the wire harness, combined with structural design such as sealed shafts and sleeve components, to ensure a protection level of IP67 or above.
- The material needs to pass anti salt spray and anti oil pollution tests to adapt to high humidity and high salt spray marine environments.
Pressure resistance and mechanical stress resistance
- The outer layer of the cable should have wear-resistant and anti extrusion properties to avoid mechanical collisions or long-term vibrations in the cabin that may cause cable damage.
- When designing, it is necessary to control the bending radius of the wire harness to avoid excessive bending that affects transmission performance.
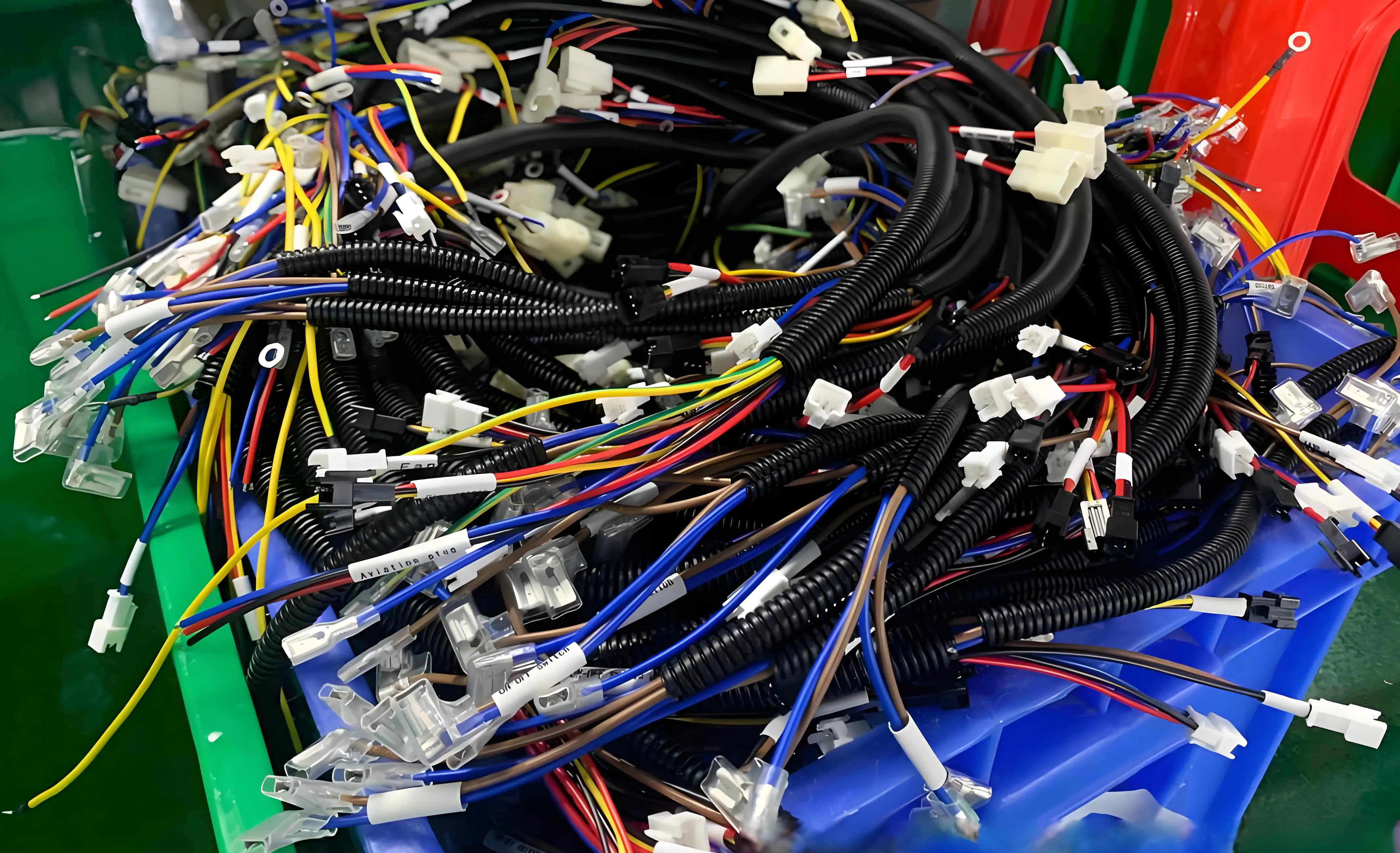
2、 Material and Performance Requirements
Cable selection
- High conductivity and high temperature resistant materials (such as copper core cables) should be used for power transmission lines, and shielded coaxial lines or optical fibers should be prioritized for signal cables to reduce electromagnetic interference.
- Hydraulic pipelines and sheaths need to be resistant to oil, acid and alkali, and avoid chemical corrosion.
Fire and explosion prevention
- The outer material of the wiring harness must comply with the ship's fire protection regulations, and its flame retardant performance must be certified by the industry (such as classification society standards).
- Explosion proof connectors should be used in critical areas such as the engine compartment to prevent accidents caused by electric sparks.
3、 Layout and structural design
Space optimization
- Compact layout and lightweight design should be adopted according to the space constraints of the vessel to reduce the area occupied by the wiring harness.
- Wire harness fixation requires the use of card slots, limit holes, and other structures to prevent loosening or interference with other equipment.
Modularity and maintainability
- Adopting a split type sleeve and modular connector design, it is convenient for quick maintenance and replacement.
- The wiring harness label should clearly indicate the function and direction, simplifying the troubleshooting process.
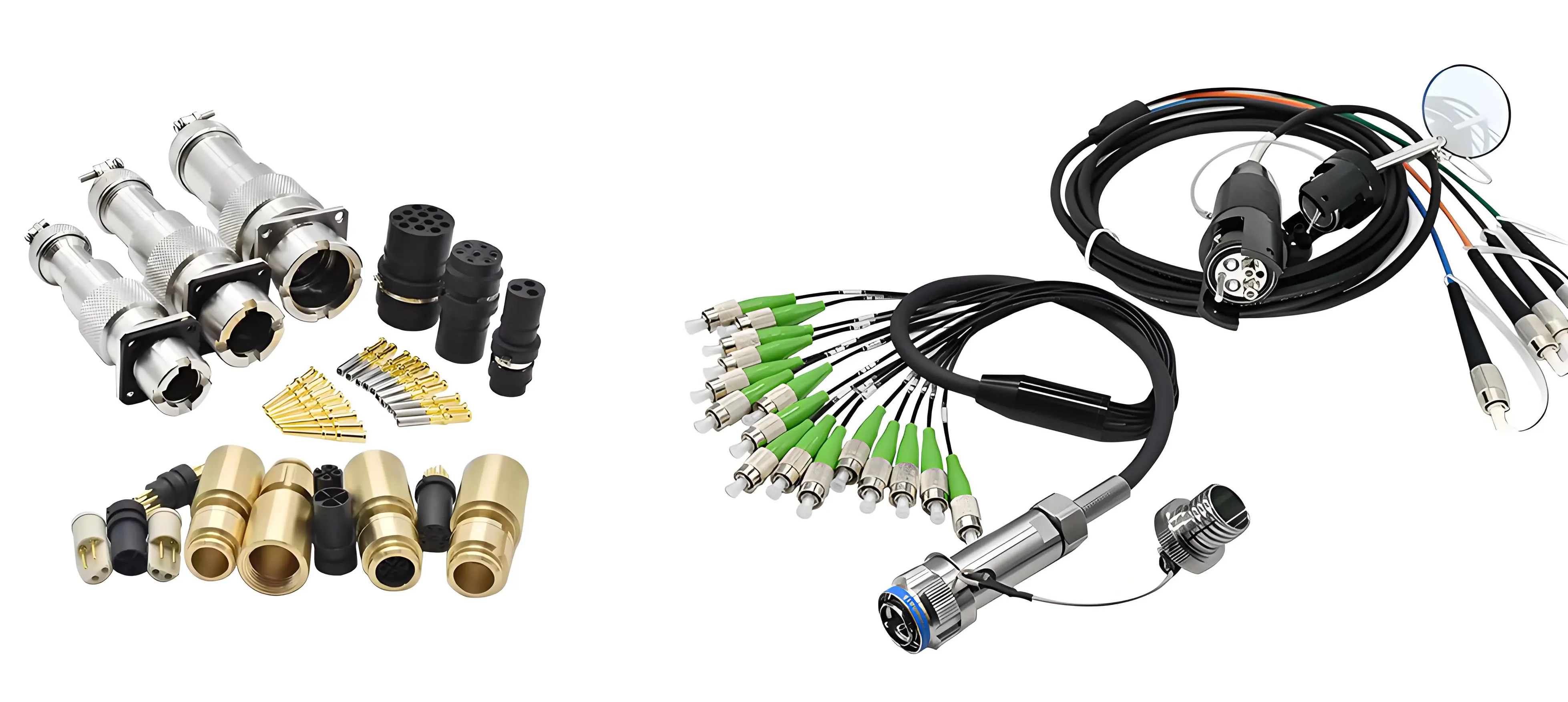
Difference from other wiring harnesses
Compared to ordinary industrial wiring harnesses, marine wiring harnesses emphasize more on waterproof sealing and corrosion resistance, and need to comply with ship industry standards, while automotive or aviation wiring harnesses focus on characteristics such as vibration resistance and high temperature resistance.
summarize
The design of marine wiring harnesses requires a comprehensive consideration of environmental tolerance, material properties, spatial layout, and safety regulations, with a focus on addressing unique ship challenges such as waterproofing, corrosion resistance, mechanical stress resistance, fire and explosion prevention.