By Admin
2024-12-09 01:31:43
What is the operation instruction for Automobile top frame and instrument harness Assembly?
Matters needing attention
- All wiring harnesses are required to be neatly wired, firmly fixed, no shaking overhang, no interference force, and no friction damage. In order to make use of various types and sizes of fixed brackets when wiring the wiring harness layout is reasonable and beautiful, the specific installation position of various electrical components and connectors should be fully considered when laying the wiring harness, and the length of the wiring harness should be combined with the body structure. For the wiring harness that grows out of the car body and is not used, it should be folded, the plug joint should be sealed and protected, and there should be no dangling or bearing force on the car body.
(The outer sheath of the wire harness must not be broken, otherwise it must be wrapped and fastened with tape or cable ties after wrapping the bellows).
- The docking of the main harness with the chassis, the docking of the top frame harness with the main harness, the docking of the chassis harness with the engine harness, the docking of the top frame harness with the rear tail harness, and the diagnostic jack of the electric control harness must be placed in a place that is easy to repair.
(At the same time, the connectors of various wiring harnesses should be placed near the access port convenient for maintenance personnel when the wiring harnesses are tied and fixed).
- When the wiring harness passes through the hole, it must be protected by a threading sheath (if there is no suitable threading sheath, it can be replaced by a corrugated pipe or black rubber, but it should be fixed firmly and not fall off), and it should be filled with sealant through the hole of the body to avoid dust entering the interior of the car. When the wire harness passes the corner edge, it should be covered with rubber skin or floor leather protection, and when it is protected by floor leather, it should be the same or similar color to the surrounding color when it is easy to see the outside leak or open the hatch door.
- In the mass production of vehicles, if there are operation instructions, the requirements of the operation instructions should be strictly followed. In the absence of operation instructions, the installation should ensure the consistency of production from the fixed position, fixed mode, and number of fixed points of the wiring harness.
- Avoid high temperature (exhaust pipe, air pump, etc.), easy moisture (lower engine area, etc.), and easy corrosion (battery base area, etc.).
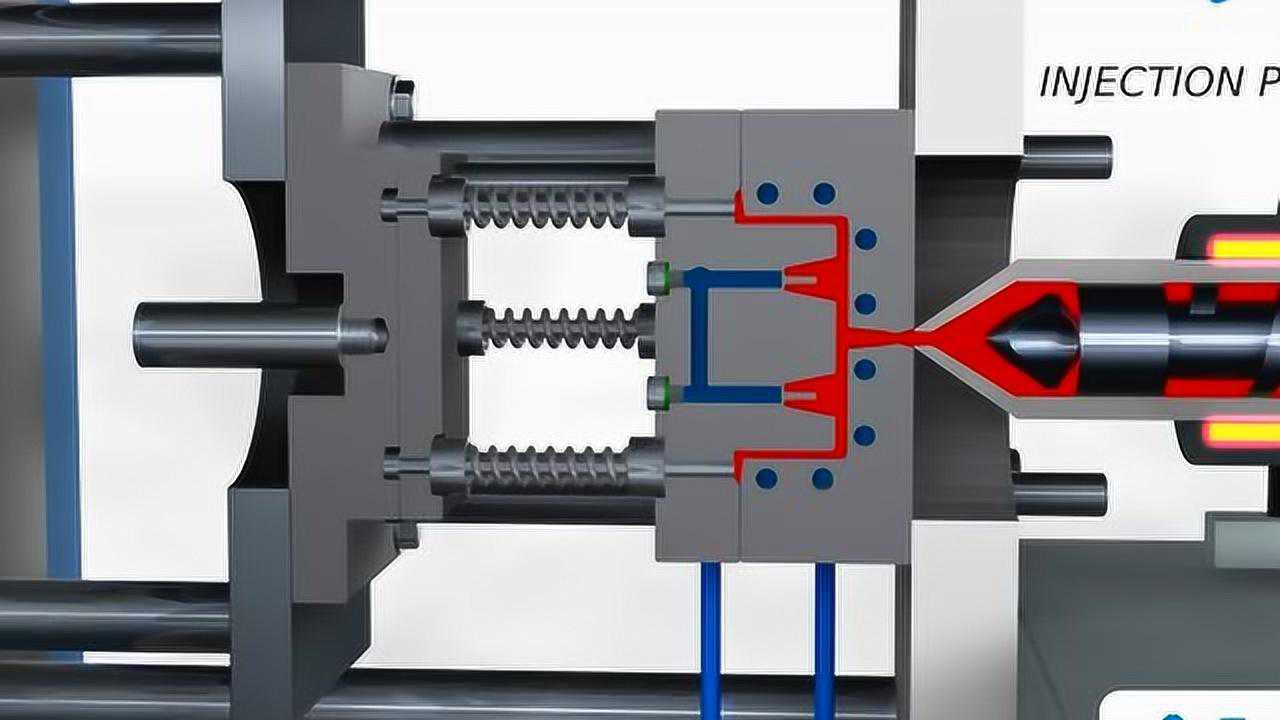
一、Top frame harness
Process content:
- The wire harness of the top frame runs along the wire hole of the large top skeleton; The wiring harness of the reading light and the wiring harness of the overhead air conditioner are fixed in the air duct with the body wire clip (the wiring harness with the baggage bracket is bound with the cable tie on the baggage bracket, and the wiring harness must walk on the upper surface of the profile under the baggage bracket hanger; when the lower bracket has a vertical profile, the wiring harness is routed from the inside of the lower profile (that is, the side window side and then fixed on the surface of the lower profile of the hanger). Avoid affecting the installation of the transition plate on the lower closure plate of the luggage rack. Follow the driver’s door post (most buses are behind the driver’s door post) to the main line bundle interface).
- When the distance between the top beam is large, the wire harness of the top frame should be fixed with a special wire card (coated 100*13) 3758-00005.
Note:
- The driver’s wiring harness installation direction on the right side of the exit car is opposite to the left and right side of the same model car in China.
Technological parameter:
- The wiring harness at the plug-in should have an active margin (30 ~ 50)mm
- Both ends (30 to 50 mm) of the insert must have fixed points.
- The spacing of two fixed points on the baggage support is (300 ~ 400)mm, and the spacing of other fixed points is not more than 700mm.
- The sag of wiring harness is not less than 10mm.
Quality requirements:
- When wiring harness is connected with electrical appliances, a certain margin should be left;
- The insertion body should not be stressed, and should not be pulled too tight or too loose.
- The distance between fixed points of the wiring harness is appropriate.
- The top frame harness is not allowed to walk inside the heat insulation board!
- When the cable card is fixed, roll up the winding bundle of the cable card and push the bracket with your hand to ensure that there is no relative movement between the cable bundle and the cable card, rather than simply bending the cable card up. The clamp should be properly flattened so that the harness and it have no displacement, and should not sag significantly.
- The wiring harness shall be flat and straight, not lower than the lower plane of the profile, and the excess growing wiring harness shall be folded neatly and fixed firmly.
- There should be no interference friction between the top wind window wiring harness and the moving parts of the top wind window pushing rod, the spacing should be at least (30~50)mm, and there should be enough activity margin (according to the amount of activity of the top wind window pushing rod in the two states of the switch), the wire harness should not be load-bearing and the wire harness should not be squeezed when pushing and pulling.
- Channel lights, horns, door lights, driver lights, reading lights, decorative lights, height lights and other electrical products can not be squeezed wire harness during installation, especially for the need to open holes in the field is strictly prohibited to damage the wire harness.
- The profile hole of the top frame harness must have a matching threading sheath.
Technological parameter:
- The length of the threading sheath must not be greater than 10mm through the profile hole.
Quality requirements:
- Threading sheath does not allow the phenomenon that only one side passes through the profile and the other end falls in the middle of the profile, nor does it allow the threading sheath to be too long and the wiring harness is sandwiched in the sheath gap.
- The wiring harness is inserted correctly according to the line color and line number.
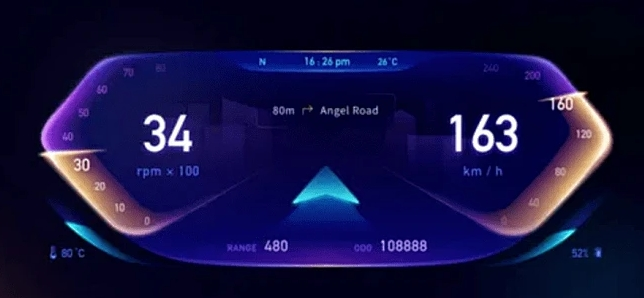
Quality requirements:
The ground cable of the air conditioner should be firmly fixed with flat washers and spring washers.
二、Instrument main wire harness
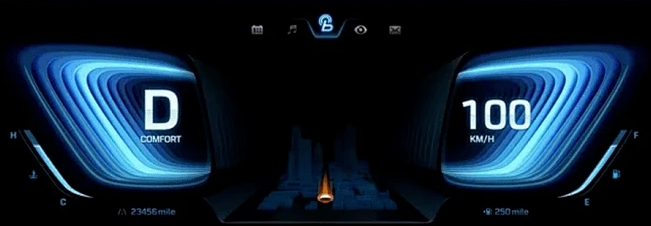
Process content:
- In general, plastic cable ties are used to secure the main cable to the front instrument beam. If the cable tie cannot be fixed, you must use the instrument cable clamp or body cable clamp (use the electric drill to drill holes in the front instrument beam, and fix the body cable clamp or instrument cable clamp to the beam, so as to fix the wire harness).
Technological parameter:
- The distance between fixed points must not be greater than 200mm.
Quality requirements:
- The distance between fixed points of the wiring harness is appropriate. The wiring harness should be arranged neatly. A maintenance allowance of at least 150mm should be left in the length of the wiring harness, and the reserved branch wiring harness should be stacked neatly and tied securely with cable ties.
- When fixing the wiring harness, it is necessary to consider that the damage of the wiring harness should not be squeezed when installing the instrument panel and other components, and the operation of opening holes and nailing should be considered to protect the wiring harness so that it can not be damaged.
- Protect sharp parts such as the instrument table bracket.
- Prevent the wire harness from being cut, and add PE plate protection if necessary.
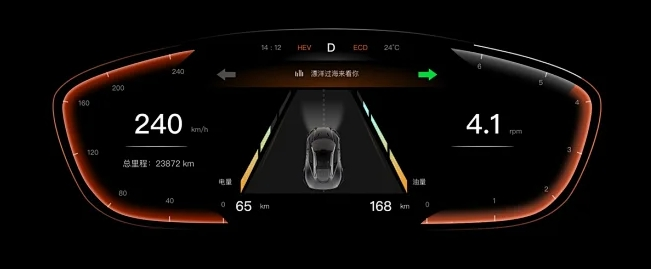
- There should be a gap between the wiring harness and the moving parts to avoid interference and friction with the moving parts (such as: wiper transmission rod, throttle control, clutch control, brake control).
Technological parameter:
Quality requirements:
- Do not interfere with moving parts. Do not shake or rub the wiring harness.
- When the wiring harness is connected to the electrical appliance, the wiring harness should leave a certain margin.
Technological parameter:
- No force at the joint, active margin (30-50mm)
Quality requirements:
- After connecting the wiring harness with the electrical parts, a certain margin should be set aside to facilitate the removal and maintenance of the electrical parts. The wiring harness allowance should meet the conditions: about 100mm of the wiring harness is exposed after the electrical part is taken out of the instrument panel.
- (5) Both ends of the connector should have fixed points.
Technological parameter:
- There should be fixed points at both ends of the insert (30-50mm).
Quality requirements:
- The connector shall not be suspended, swayed, or carried.
- Correctly connect the connector body according to the line color and line number.
Quality requirements:
- The connector of the wiring harness must be replaced when it is damaged, and it is strictly prohibited to hide it and cause hidden dangers to the quality of the vehicle. The connector must be connected reliably and connected correctly, and placed near the access port that is convenient for maintenance personnel.
- The water pipe of the wiper is arranged under the front windshield, and the rubber plated wire card is used to fix it.
Technological parameter:
- The droop is less than 20mm.
Quality requirements:
- The water pipe shall not be squeezed flat to affect the normal operation of the scrubber, and the pipe shall not be too loose.
- Under the instrument harness bin floor through the hole with rubber rubber ring protection and apply black Sika rubber seal.
Technological parameter:
- In special cases, if the rubber ring is cut, the opening gap is less than 5mm.
Quality requirements:
- The size of the rubber ring matches the aperture.
- The glue is evenly coated, the seal is tight and opaque, there is no leakage or incomplete glue, and the glue should be evenly scraped on both sides of the cabin through the hole.
- Before the installation of the electrical box, the surface of the electrical box is protected with protective cloth to prevent the relay plug-in from falling off and losing, while preventing sawdust, iron slag and other debris from falling into the electrical box.
Quality requirements:
- Protect the electrical box of the vehicle during the production process to avoid sawdust, iron slag and other debris falling into the electrical box.
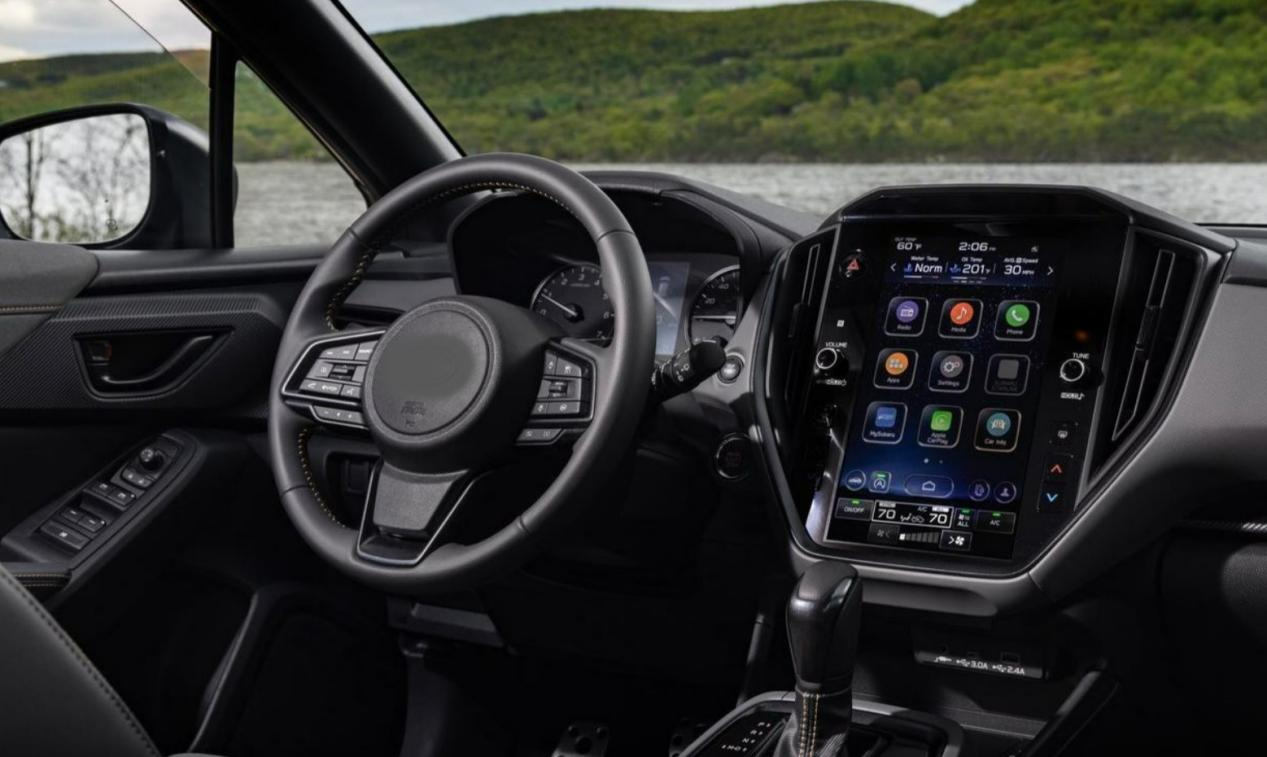
If you need any custom wiring harness, you can contact us.