By Admin
2025-03-19 01:12:40
The core points and engineering practice of automotive Wiring harness design
Wiring harness design is a critical engineering process that ensures safe and efficient electrical connectivity in vehicles.
As a key link in the integrated design of automotive electronic systems, the layout design of automotive wiring harnesses directly affects the electrical performance and reliability of the entire vehicle. As the "neural network" of automobiles, wiring harnesses must achieve efficient connection solutions for onboard electronic devices in complex environments. The following provides a detailed explanation of the technical points from design principles to the entire production process.
1. Basic principles of automotive wiring harness design
- Safety design specifications: The layout must meet the requirements of fire prevention, heat resistance, and moisture resistance, and avoid the risks of short circuits and grounding faults.
- Reliability guarantee of vehicle wiring harness: High temperature resistant and vibration resistant wires are selected to adapt to extreme working conditions of -40 ℃~125 ℃.
- Lightweight layout of automotive wiring harness: Simplify the length and joints of the wiring harness, reducing the failure rate and later maintenance costs.
- Maintainability Engineering Standard: Adopting modular design, paired with color-coded labels for quick maintenance.
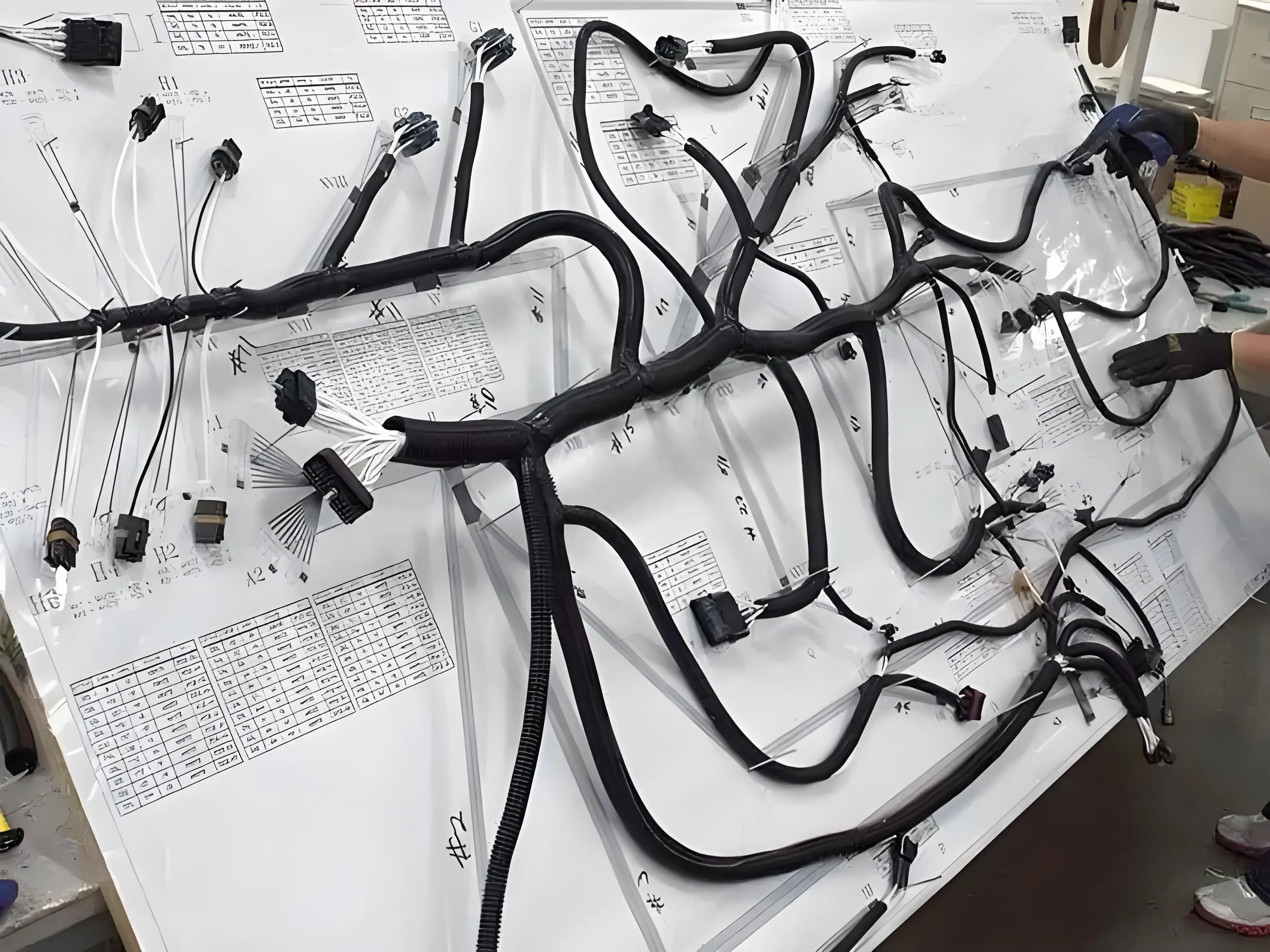
2. Optimization of Automotive Wiring Harness Layout Strategy
- Partition wiring design method: Independent wiring is used in areas such as the engine compartment and cab to avoid signal cross interference.
- Electromagnetic compatibility (EMC) protection technology: The high-frequency signal line uses a double-layer shielding layer and maintains a distance of at least 15cm from the power line.
- Lightweight solution for new energy vehicle wiring harness: using aluminum wires and thin-walled insulation materials, reducing weight by 30% compared to traditional copper wires.
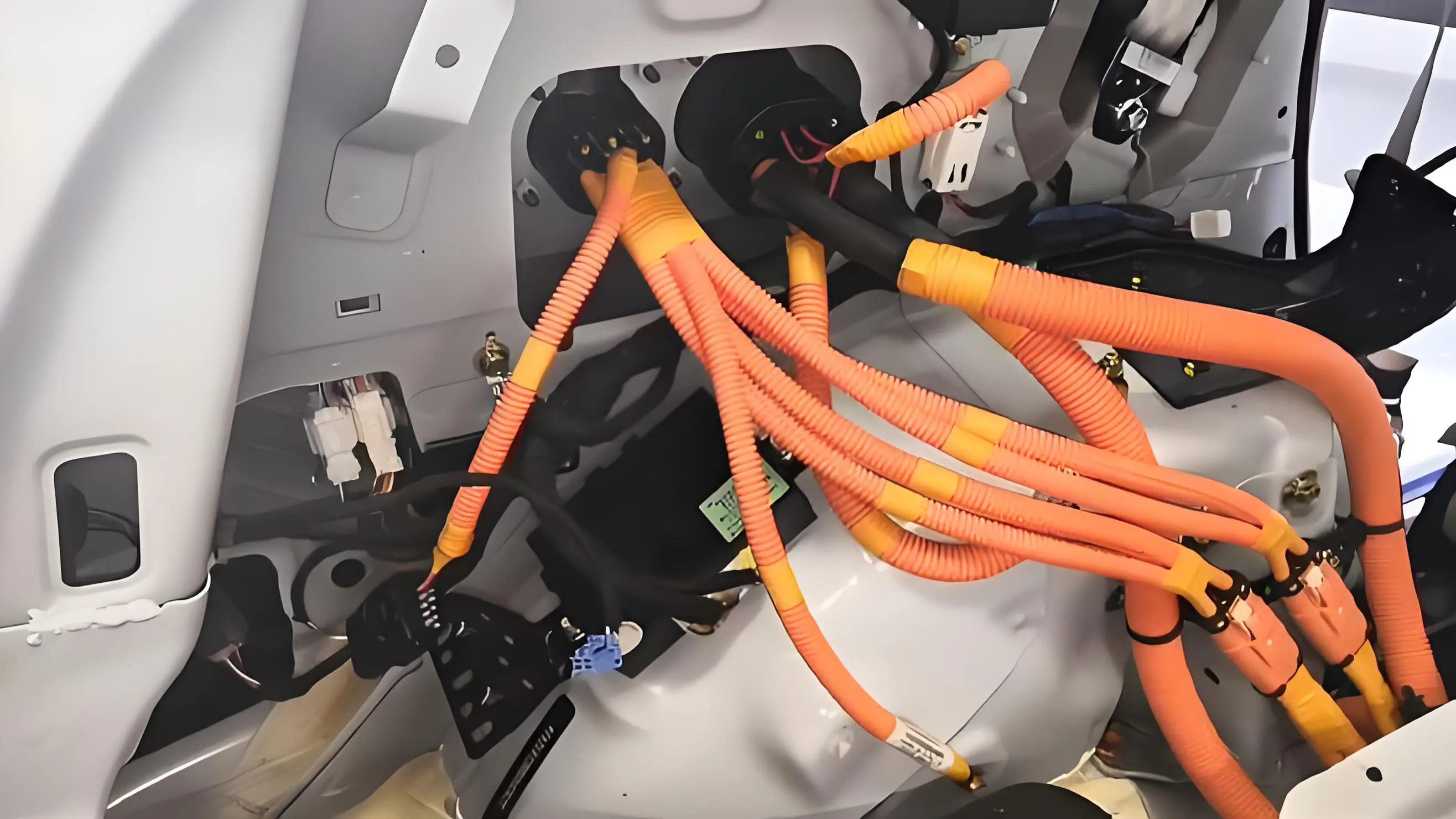
3. Key points for selecting core components of automotive wiring harnesses
- Calculation of wire specifications for car wiring harness: Match the wire diameter based on the load current (e.g. 2.5mm ² cross-sectional area required for ABS).
- Waterproof design of automotive connectors: IP67 grade sealing components with snap-on fixation to prevent vibration loosening.
- New energy vehicle high-voltage wiring harness material: Silicone rubber insulation layer can withstand high temperatures of 300 ℃ and meet the requirements of an 800V voltage platform.
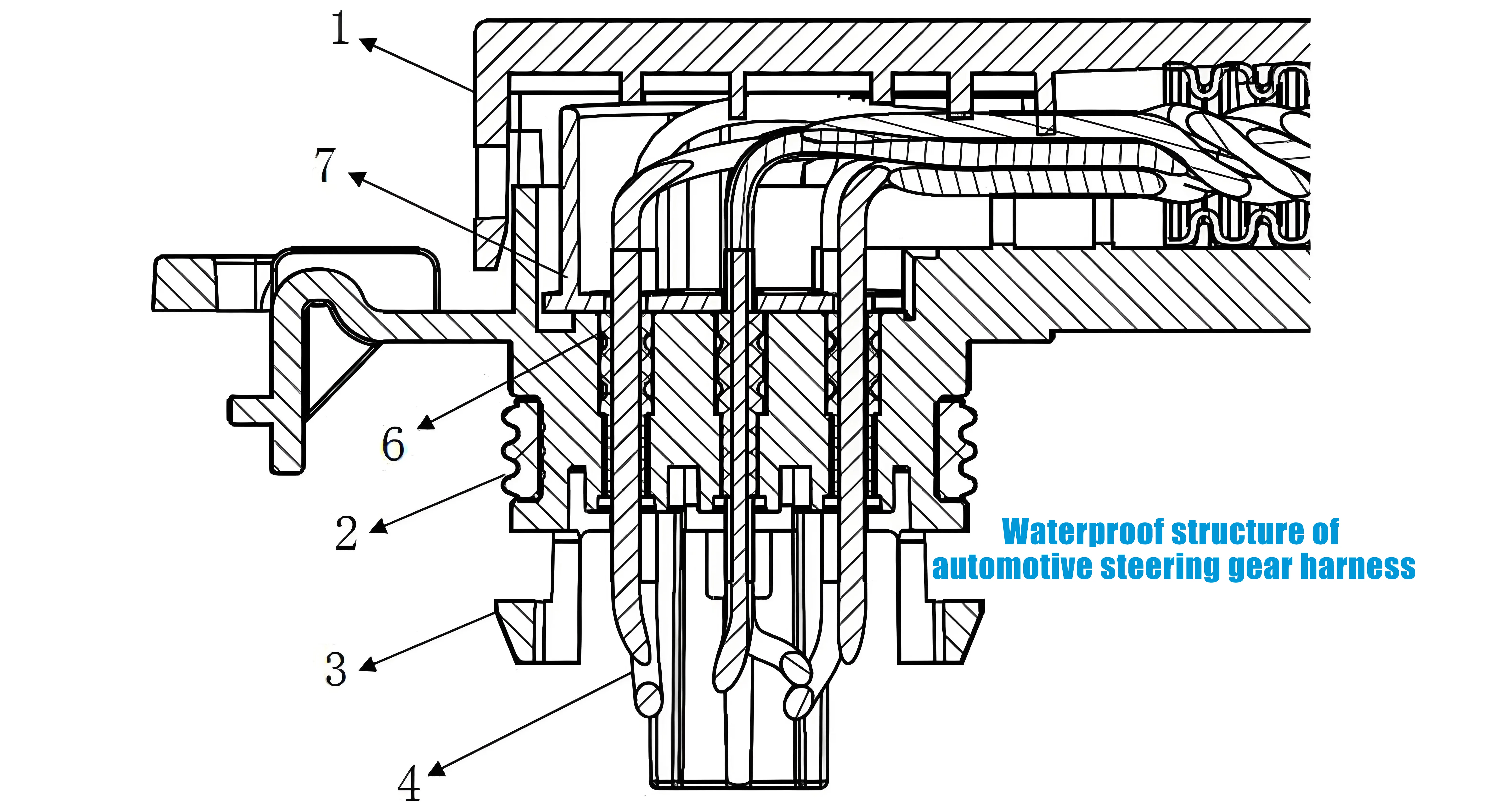
4. Complete process steps for automotive wiring harness layout
- Requirement analysis of the vehicle electrical system: Establish a power consumption and communication matrix for devices such as ECU and sensors.
- 3D wiring harness routing simulation: Use CATIA/CHS software to verify the rationality of the path and avoid interference from moving parts.
- Reliability verification of wire harness samples: Through rigorous experiments such as 100000 insertion and extraction tests and 50G mechanical impact tests.
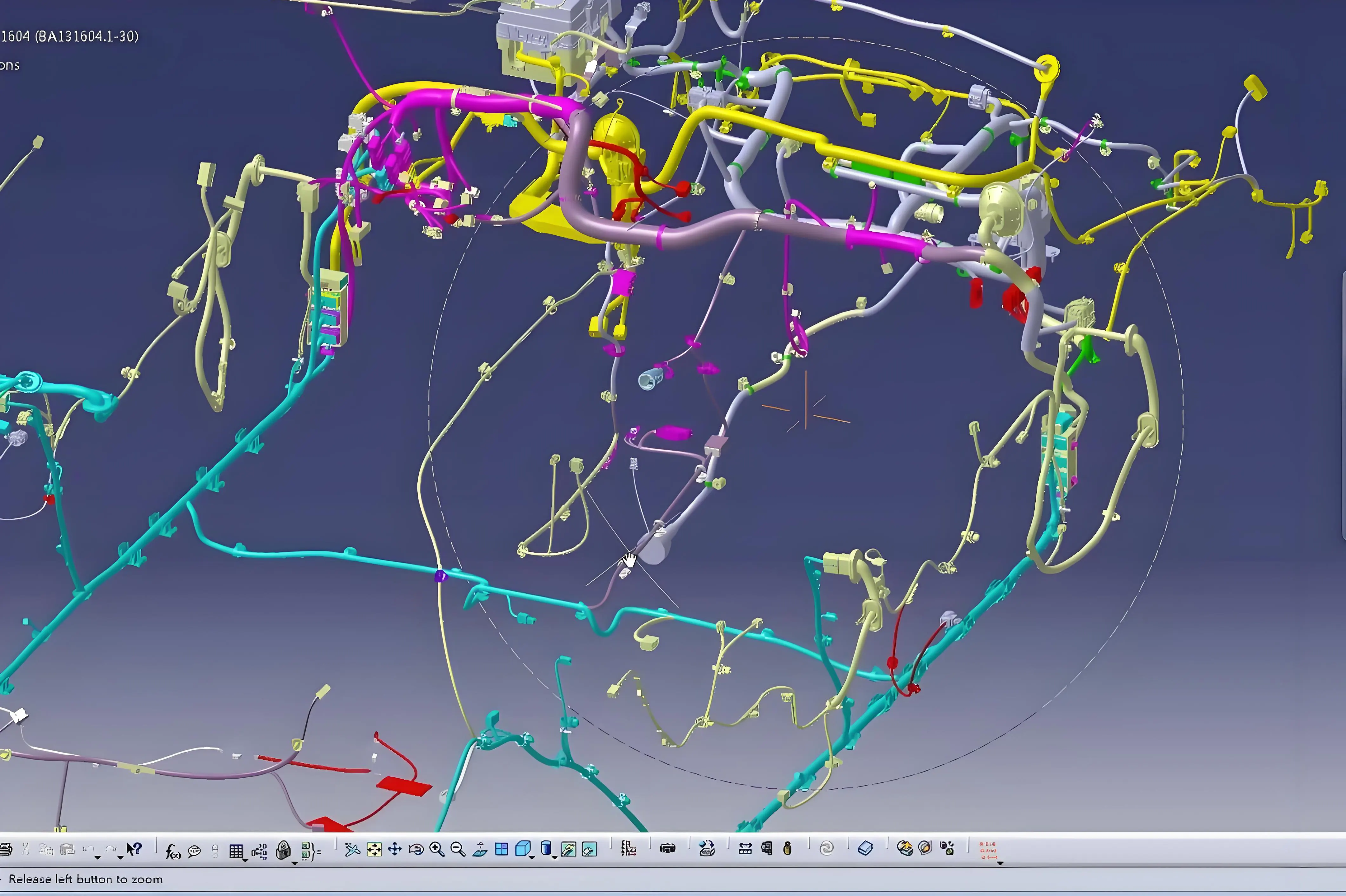
5. Key steps in automotive wiring harness testing
- Automated detection of conduction impedance: using a flying needle tester to achieve 100% circuit continuity screening.
- High voltage wire harness insulation performance test: 500V DC withstand voltage test lasts for 60 seconds, with leakage current<10mA.
- Vehicle electrical system joint debugging test: simulate rain, snow, and bumps to verify signal stability.
6. Intelligent manufacturing technology for automotive wiring harnesses
- Automated process for wire harness processing: The fully automatic cutting and crimping machine has an accuracy of ± 0.1mm and a daily production capacity of 2000 sets.
- Automotive assembly error prevention system: using RFID technology to verify wire harness codes, the assembly accuracy has been improved to 99.97%.
Conclusion
From the design specifications for high-voltage wiring harnesses in new energy vehicles to EMC solutions for intelligent driving wiring harnesses, the layout design of automotive wiring harnesses is evolving towards lightweight and high integration. Mastering these key points of automotive electronic system connection technology will effectively enhance the quality of vehicle development and market competitiveness.