By Admin
2024-12-13 06:41:58
Low Voltage Harness Wear Prevention Guide
Low-voltage wiring harness wear protection is a key link to ensure the stability of the electrical system and extend the life of the wiring harness.
Material and protective layer selection for low voltage wiring harness
Wear resistant sheath wrapping
- Priority should be given to using corrugated pipes (PP/PA material) or heat shrink tubing to wrap the wire harness, improving wear resistance and flame retardancy, suitable for high temperature and high vibration areas such as engine compartments.
- The bent parts of the branch wire harness can be wrapped with PVC sleeves or sponge tape to reduce frictional stress and absorb vibration noise.
Tape assisted protection
- Use cloth tape (temperature resistant to 150 ℃) or velvet tape to wrap the surface of the wire harness for a second time, enhancing local wear resistance.
- The chassis wiring harness needs to be isolated from the body sheet metal holes through rubber parts (made of EPDM material) to prevent contact wear and seal failure.

Wiring design and fixing specifications
Layout optimization
- The spacing between wire harness branches should be ≥ 20mm to avoid cross friction; The diameter design of the main line needs to reserve 30% of the cross-sectional area redundancy to reduce fatigue fracture caused by vibration.
- The engine compartment wiring harness should be kept away from high-temperature components (such as exhaust pipes) and protected with materials that can withstand temperatures up to 125 ℃.
Fixed and limited position
- Secure the wiring harness with a pressure plate, limit hole, or nylon zip tie to limit its displacement amplitude under dynamic vehicle conditions (recommended displacement ≤ 5mm).
- Sensitive parts (such as sensor connectors) need to be fixed with brackets or cable trays to prevent associated damage.
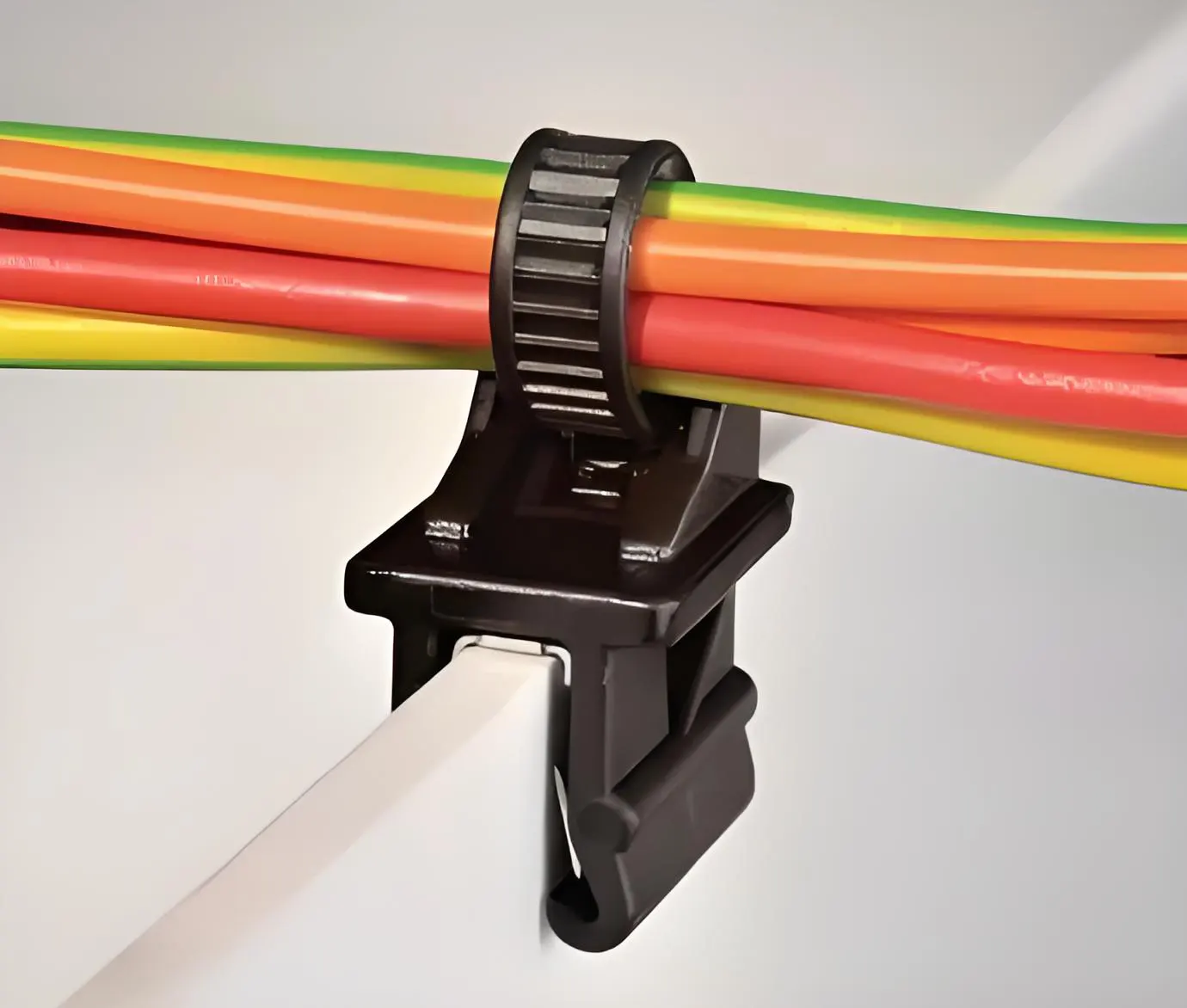
Maintenance and testing process
Regular inspection standards
- Quarterly inspection of issues such as cracked wire harness outer skin, exposed copper wires, and oxidized interfaces, with a focus on areas such as chassis and car doors that are prone to wear.
- Use visual inspection and hand touch method to determine the degree of aging of the corrugated tube (if the hardness changes by ≥ 20%, it needs to be replaced).
Cleaning and maintenance
- Use a low-pressure spray bottle to rinse during cleaning to avoid direct impact of high-pressure water gun on the wiring harness; After cleaning, spray silicon-based protective agent to form a waterproof and anti-oxidation film.
- Wet area wiring harnesses (such as bumper wiring harnesses) need to be additionally checked for compatibility between sealing plugs and blind plugs to ensure an IP67 protection level.
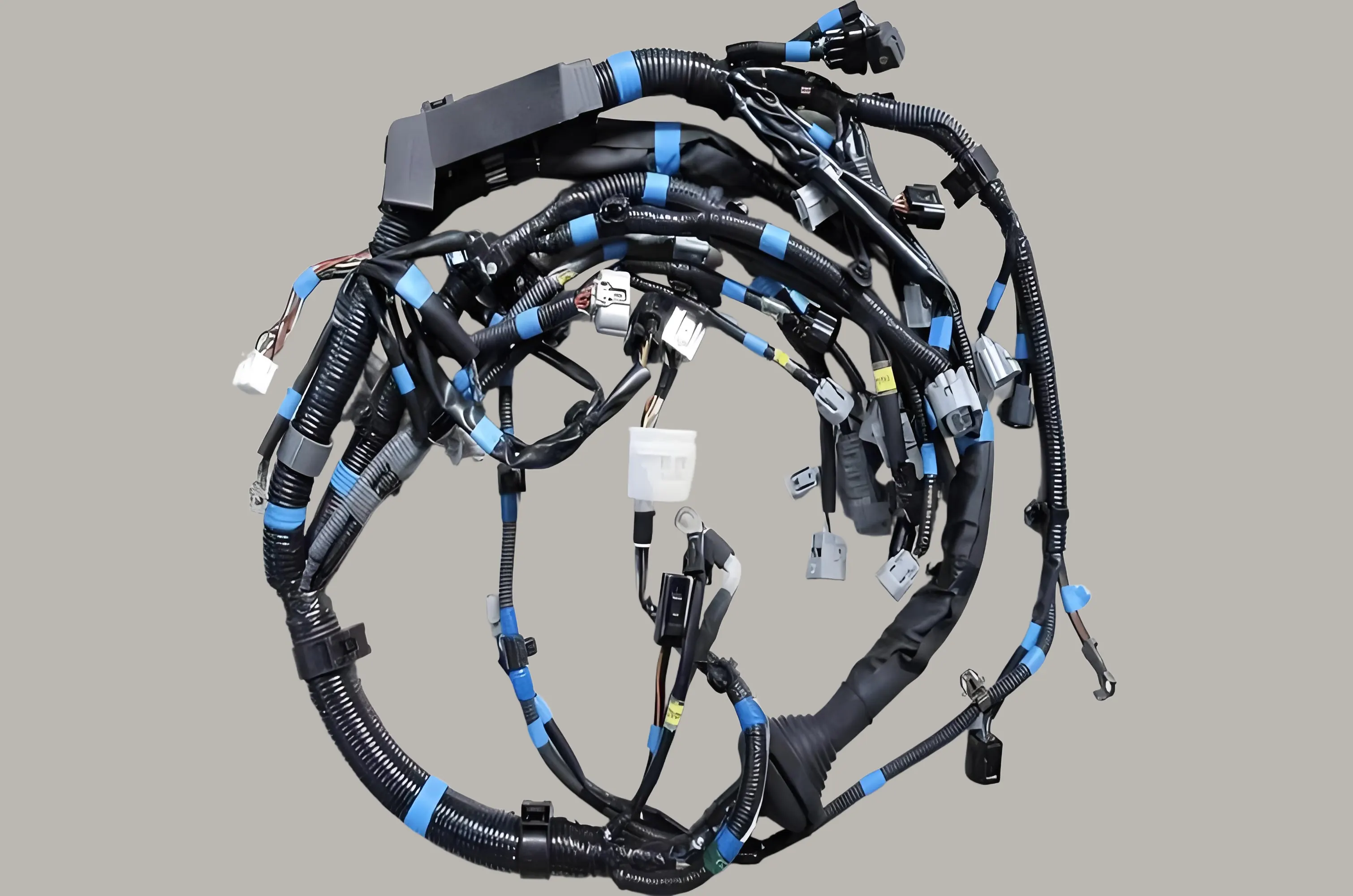
High temperature protection method for low voltage wiring harness
Protection Dimension |
Specific measures |
Implementation method |
Applicable scenarios/remarks |
Material protection measures |
Protective case application and Wear-resistant material selection |
Use corrugated tubes, heat shrink tubes or PA/PP sheaths to wrap the wiring harness. In special scenarios (such as the engine compartment), use waterproof threaded tubes or PVC tapes to seal them. |
High temperature, high vibration areas (such as engine compartment) |
Routing design optimization |
Reasonable layout and fixing |
The wiring harness is fixed by limiting holes and wire pressing plates, and 30% cross-sectional area redundancy is reserved during design. |
Avoid friction losses caused by vibration |
Maintenance and testing specifications |
Regular inspection and cleaning |
Check for cracks in the outer covering and exposed copper wires, and clean the wiring harness using a low-pressure spray bottle and a neutral detergent. |
Check every quarter |
Through the above method, the failure risk of low-voltage wiring harness in high temperature environment can be effectively reduced, the service life can be extended and the system safety can be guaranteed.