By Admin
2025-02-22 02:29:36
electronics wire harness
Core Processes in Wire Harness Production
1. Design and Engineering
The foundation of a high-quality wire harness lies in robust design. Engineers use CAD software (e.g., AutoCAD, Zuken E3) to create schematics that optimize space, reduce interference, and meet application-specific requirements. For example:
- Automotive: Designs adhere to SAE J1128 and Ford ES-XU1T-1A278-AC standards for vibration resistance.
- Medical: Schematics prioritize signal integrity and sterilization compatibility.
Prototyping follows, with 3D-printed mockups to validate fitment and electrical performance.
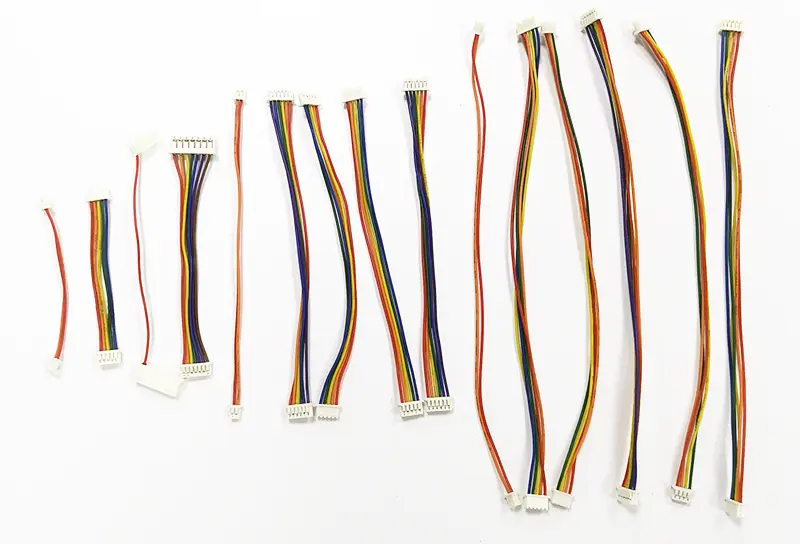
2. Material Selection and Sourcing
Material choice directly impacts durability and compliance:
- Conductors: Oxygen-free copper (OFC) for minimal resistance; silver-plated wires for high-frequency medical devices.
- Insulation: Automotive harnesses use cross-linked polyethylene (XLPE) for heat resistance (-40°C to 150°C), while medical-grade assemblies require PTFE for biocompatibility.
- Connectors: Industry-standard components like Molex MX150 (automotive) and JST SMH (medical) ensure secure, corrosion-resistant connections.
3. Wire Cutting and Stripping
Laser-guided machines cut wires to lengths with ±0.1mm precision. Automated stripping removes insulation without damaging conductors, critical for high-voltage EV harnesses or delicate medical sensors.
4. Termination and Crimping
Hydraulic crimping tools apply 12–20 kN force to attach terminals (e.g., Deutsch DT, JST VH), ensuring gas-tight connections. Automated optical inspection (AOI) verifies crimp height and pull strength, meeting IPC 620 Class 3 standards.
5. Shielding and Protection
- EMI/RFI Shielding: Braided copper or aluminum foil wraps protect automotive ADAS systems from interference.
- Jacketing: Silicone or thermoplastic polyurethane (TPU) jackets provide abrasion resistance for industrial robots.
6. Assembly and Integration
Wires are routed on modular formboards or automated guided vehicles (AGVs). Modular designs allow for scalable production of custom cable assemblies, such as:
- EV Charging Harnesses: Integrating SAE J1772 connectors with liquid-cooled cables.
- Surgical Tool Cables: Coaxial wiring for electrosurgical devices with ISO 10993-certified materials.
7. Testing and Validation
- Electrical Testing: Continuity, insulation resistance (min. 100MΩ at 500VDC), and hi-pot (1.5kV AC for 60 seconds).
- Environmental Testing: Thermal cycling (-40°C to 125°C), salt spray (per ASTM B117), and IP67 waterproof validation.
- Certifications: IATF 16949 (automotive), ISO 13485 (medical), and UL/CSA listings.
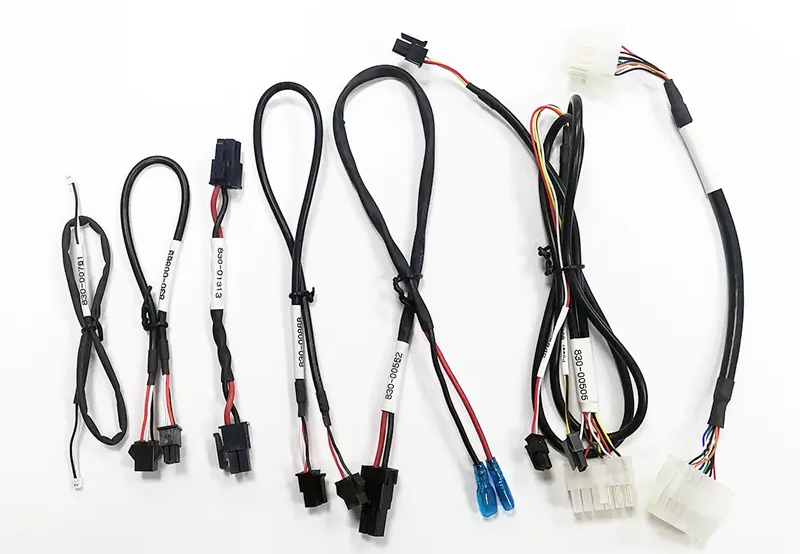
Industry-Specific Differentiation
Automotive Wire Harness Design Guide
- High-Voltage Systems: EV harnesses use orange XLPO insulation and shielded twisted pairs for CAN bus communication.
- Lightweight: Aluminum conductors reduce weight by 50% vs. copper, critical for EVs.
- Modularity: Plug-and-play designs simplify repairs in vehicles like trucks and tractors.
Medical-Grade Custom Cable Assembly
- Sterilization Compliance: Ethylene oxide (EtO)-resistant materials for reusable surgical tools.
- Signal Accuracy: Coaxial cables with 95% shielding effectiveness for MRI machines.
Industrial Automation Solutions
- Robotic Harnesses: Continuous-flex cables with 10 million bend cycles (per IEC 60227-6).
- Renewable Energy: UV-resistant MC4 connectors for solar panel arrays.