Von Admin
2025-02-22 02:29:36
Elektronik Wire Harness
Kernprozesse in der Wire Harness Produktion
1. Design und Engineering
Die Grundlage eines hochwertigen Drahtgürts liegt in einem robusten Design. Ingenieure verwenden CAD-Software (z.B. AutoCAD, Zuken E3) zur Erstellung von Schematiken, die den Raum optimieren, Störungen reduzieren und anwendungsspezifische Anforderungen erfüllen. Zum Beispiel:
- Automotive: Die Designs entsprechen den SAE J1128 und den Ford ES-XU1T - 1A278 - AC-Standards für die Vibrationsbeständigkeit.
- Medizinisch: Schematische Prioritäten legen auf Signalintegrität und Sterilisationskompatibilität.
Es folgt das Prototyping, mit 3D-gedruckten Mockups, um die Anpassung und die elektrische Leistung zu validieren.
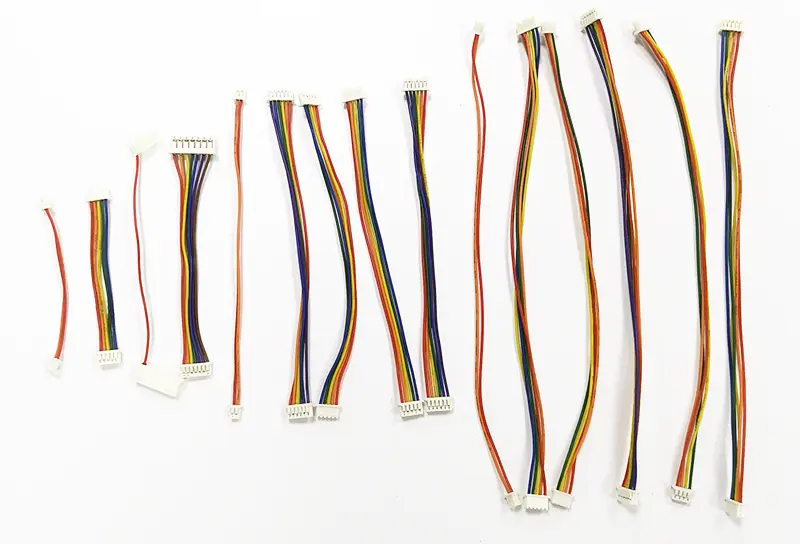
2. Materialauswahl und Sourcing
Die Materialauswahl wirkt sich direkt auf Haltbarkeit und Compliance aus:
- Leiter: Sauerstofffreies Kupfer (OFC) für einen minimalen Widerstand; silberplatte Drähte für Hochfrequenzmedizinische Geräte.
- Isolation: Automobil-Gürte verwenden vernetztes Polyethylen (XLPE) für die Wärmebeständigkeit (-40 ° C bis 150 ° C), während medizinische Baugruppen PTFE für die Biokompatibilität benötigen.
- Steckverbinder: Industriestandardkomponenten wie Molex MX150 (Automotive) und JST SMH (Medical) sorgen für sichere, korrosionsfeste Verbindungen.
3. Wire Cutting und Stripping
Lasergeführte Maschinen schneiden Drähte mit ± 0,1 mm Präzision auf Längen. Das automatisierte Stripping entfernt die Isolierung, ohne Leiter zu beschädigen, was für Hochspannungs-EV - Gärten oder empfindliche medizinische Sensoren entscheidend ist.
4. Termination und Crimping
Hydraulische Crimping-Werkzeuge anwenden 12â 20 kN Kraft zum Befestigen von Anschlüssen (z. B. Deutsch DT, JST VH), die gasdichte Verbindungen gewährleisten. Die automatische optische Inspektion (AOI) überprüft die Crimp-Höhe und die Zugfestigkeit und erfüllt die Normen IPC 620 Klasse 3.
5. Shielding und Schutz
- EMI / RFI-Abschirmung: Gefleckte Kupfer - oder Aluminiumfolie-Hüllen schützen ADAS-Systeme vor Störungen in der Automobilindustrie.
- Jacke aus Silikon oder thermoplastischem Polyurethan (TPU) bieten Abriebfestigkeit für Industrieroboter.
6. Versammlung und Integration
Die Drähte werden auf modularen Formplatten oder automatisierten geführten Fahrzeugen (AGVs) geleitet. Modulare Designs ermöglichen eine skalierbare Produktion von kundenspezifischen Kabelbaugruppen, wie:
- EV Charging Harnesses: Integration von SAE J1772 - Steckverbindern mit flüssiggekühlten Kabeln.
- Chirurgische Werkzeugkabel: Koaxiale Verkabelung für elektrochirurgische Geräte mit ISO 10993 - zertifizierten Materialien.
7. Tests und Validierung
- Elektrische Prüfungen: Kontinuität, Isolierungswiderstand (min. 100MΩ bei 500VDC) und Hi-Pot (1,5 kV AC für 60 Sekunden).
- Umweltprüfung: Thermisches Zyklusverfahren (-40 ° C bis 125 ° C), Salzspray (nach ASTM B117) und IP67 - Wasserdichtigkeitsvalidierung.
- Zertifizierungen: IATF 16949 (Automotive), ISO 13485 (Medizinische) und UL / CSA-Listen.
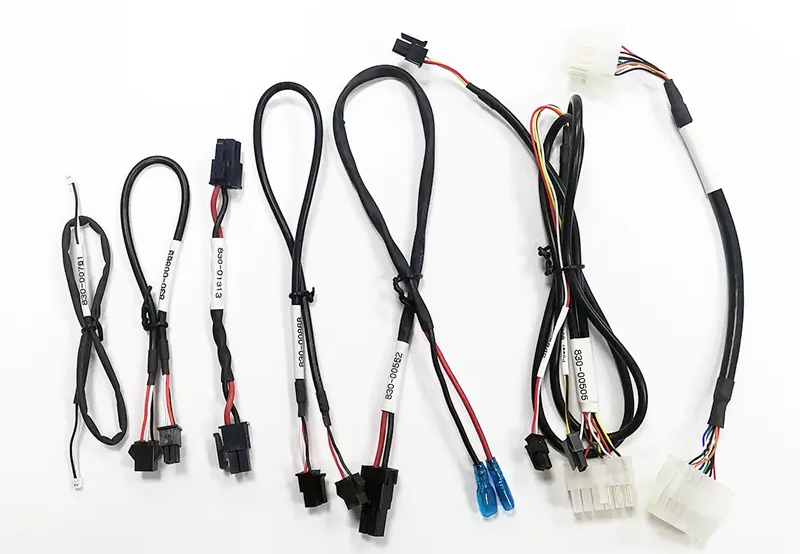
Branchenspezifische Differenzierung
Automotive Wire Harness Design Guide
- Hochspannungssysteme: EV-Gärten verwenden orangefarbene XLPO-Isolierungen und abgeschirmte Twisted Pairs für die CAN-Bus - Kommunikation.
- Leichtgewicht: Aluminiumleiter reduzieren das Gewicht um 50% gegenüber Kupfer, was für Elektrofahrzeuge entscheidend ist.
- Modularität: Plug-and - Play-Designs vereinfachen Reparaturen in Fahrzeugen wie Lastwagen und Traktoren.
Medizinische Qualität Custom Cable Assembly
- Sterilisation Compliance: Ethylenoxid (EtO) - resistente Materialien für wiederverwendbare chirurgische Instrumente.
- Signalgenauigkeit: Koaxkabel mit 95% Abschirmwirksamkeit für MRT-Maschinen.
Lösungen für industrielle Automatisierung
- Robotergürne: Continuous-Flex - Kabel mit 10 Millionen Biegezyklen (nach IEC 60227 - 6).
- Erneuerbare Energien: UV-resistente MC4 - Steckverbinder für Solarpanel-Arrays.